I am returning to the hobby after a while… currently, I am working on Aeropoxy’s Ikarus IK-2 in quarterscale. To the best of my knowledge, it’s the only kit of this interesting aircraft in this scale. I hope to post some photos of the build, too. However, this was not a reason to write the post. Cherishing all the advantages (and disadvantages) of a short-run resin kit – besides the zillion of bubbles and the rest – I encountered a problem which sparkled some imagination. The IK-2, being a pre-WWII fighter, has some nice fabric covered surfaces which I wanted to reproduce. I simply didn’t like the original resin casting, which was a bit too pronounced and overdo. First I tried some fine sanding and chiseling with the rounded Micro-Chisel tip, but I ended up with some deep trenches in the resin. I wish I hadn’t tried so much! Nevertheless, now I needed a quick and effective solution… I intended to fill the trenches and give it a smooth-sand back to normal, but then an idea came across my mind. I simply had to give it a try, and I wanted to share this with you.
Well, if you ever thought about reproducing a fabric cover effect in this scale, this might be helpful. I dug out the old MS.406, which ended up in the scrapheap never to be lifted again, and tried the following. If you have a pack of Kleenex or any other cellulose tissue at hand, you’ll notice that they are comprised of several thin cellulose layers. First remove a layer or two, and cut it in desired shape (don’t cut them with your hobby-knife blade, because it will tear the fabric; a pair of sharp and pointed fisherman’s scissors will work just fine). Then place the tissue on plastic or resin and water it thoroughly with a brush. Remove the excess water, and help the tissue set on the surface. Dip your brush in somewhat diluted Micro Kristal Klear, and apply it gently to the surface. (I also tried the Gator’s Grip glue, but the final result looks better with the former, because it seals the tissue into a nice and silky finish.) If necessary, repeat the procedure until the desired effect is finally reproduced. I haven’t tried it yet, but I guess it might look just fine after some cleanup and a coat of primer. I hope I will manage to post some photos as well. So, tell me what you think?
PS. Please bear with my English...
World War II
Discuss WWII and the era directly before and after the war from 1935-1949.
Discuss WWII and the era directly before and after the war from 1935-1949.
Hosted by Rowan Baylis
Reproducing the fabric effect on your kit?
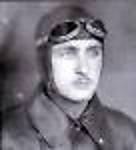
eseperic

Joined: November 06, 2009
KitMaker: 624 posts
AeroScale: 609 posts
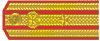
Posted: Friday, August 20, 2010 - 05:00 AM UTC

ShawnM

Joined: November 24, 2008
KitMaker: 564 posts
AeroScale: 510 posts

Posted: Friday, August 20, 2010 - 05:33 AM UTC
I've thought about this as well, although I have not tried it yet.
Please post some pics when you do try it out.
p.s.
your English is just fine!
Please post some pics when you do try it out.
p.s.
your English is just fine!
Removed by original poster on 08/20/10 - 18:01:03 (GMT).
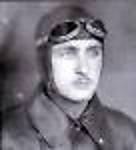
eseperic

Joined: November 06, 2009
KitMaker: 624 posts
AeroScale: 609 posts
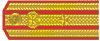
Posted: Friday, August 20, 2010 - 07:03 AM UTC
Well, I don't have a better camera at hand, but you should get an impression of what I mean... I applied another coat of diluted Gator's glue, and it set just fine. Maybe a coat of Mr.Surfacer 1200 will help to correct minor deficiencies, but it looks just fine without it. I will definitely try it on the IK-2, but I first must reproduce the lost ribs... Will post the results.
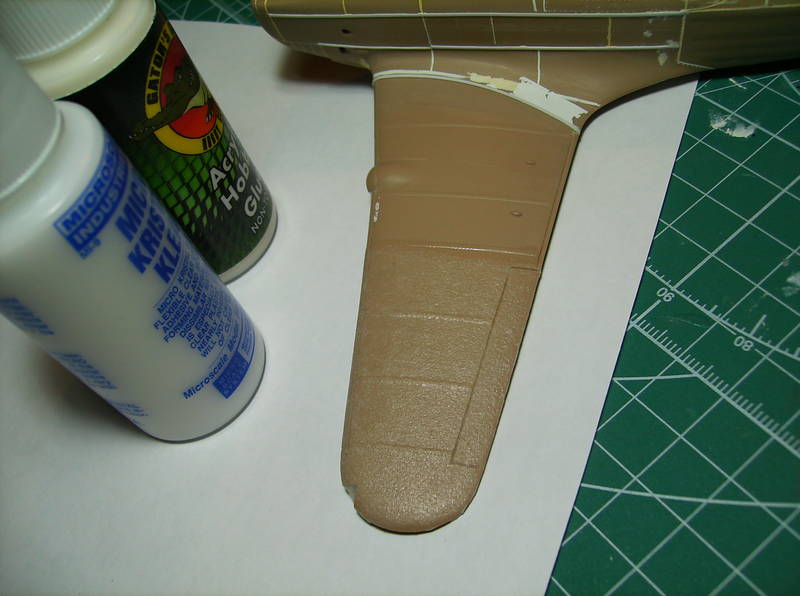
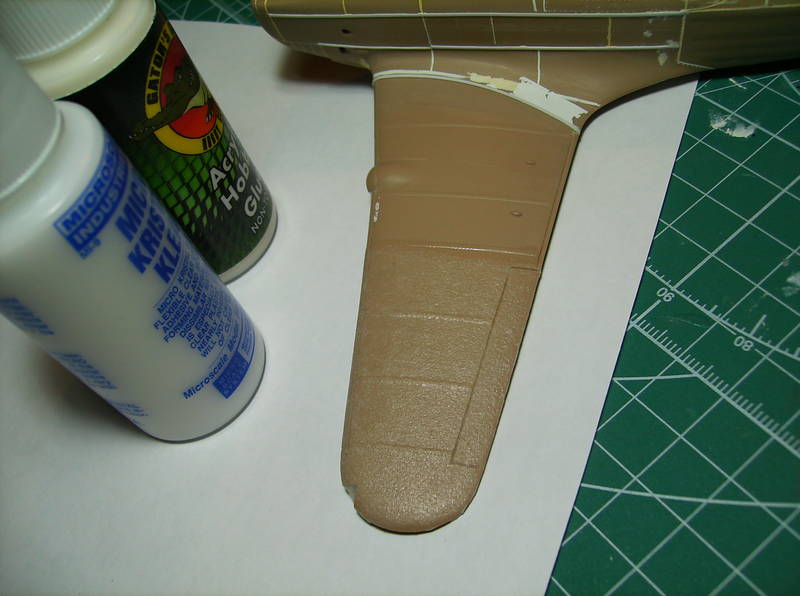

EdgarBrooks

Joined: June 03, 2006
KitMaker: 397 posts
AeroScale: 384 posts

Posted: Friday, August 20, 2010 - 06:28 PM UTC
For what it's worth (and I suspect that it'll be ignored,) my advice is to forget it. Inspect any fabric-covered surface, that's been properly finished, and you'll see a perfectly smooth, almost glass-like, finish. The purpose of the dope is to fill the "grain" of the fabric, and make it water, and air, tight. During the war, when applications were made as few as possible, to save materials, fabric was still given a minimum of 5 coats of shrinking dope; this means that all sign of the weave disappeared. Think bigger; if your "reworking" of the surface leaves grooves even .5mm deep, in 1/48 this equates to 24mm, or virtually 1 inch, and there's no fabric, in existence, that thick.
Edgar
Edgar
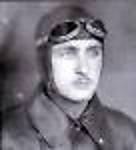
eseperic

Joined: November 06, 2009
KitMaker: 624 posts
AeroScale: 609 posts
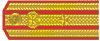
Posted: Friday, August 20, 2010 - 08:35 PM UTC
Edgar, to be honest, I was thinking about that as well. This was "invented" only to fix the problem, but I can imagine what you are saying. It sounds reasonable... Although I cannot think of the possible use of this technique, it seemed quite interesting, and it provides some interesting results. There are many fabric and textured surfaces besides the airplane. I practiced a bit, and I can say that you can easily reproduce a decent fabric effect... it might be utilized for various diorama settings - fabric chairs, covers etc. Diluted Micro Kristal Klear or Gator's glue really seal the tissue nicely, and you can even form it in different shapes and sizes. But I agree: maybe the fabric effect on the aircraft wasn't a good idea at all...

gaborka

Joined: October 09, 2005
KitMaker: 626 posts
AeroScale: 264 posts

Posted: Friday, August 20, 2010 - 09:59 PM UTC
Maybe you could make a fabric effect by painting the fabric surfaces a bit different in color and adding a very flat varnish (like Gunze flat acrylic)? This way you don't overdo the texture and have the right scale effect but still indicate that the surface is a different material.

![]() |