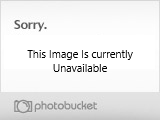
Hi everyone
This blog is going to test a theory. The theory is that paint is more important than plastic. In other words an average kit can be made to look great with a decent paint job, plus some care and skill in assembly and a little scratch building. It’s not necessary to buy lots of highly detailed after market goodies to end up with a very pleasing and detailed looking end result.
Of course in an ideal world there’d be no need to choose — yes, I’ll have all the aftermarket goodies as well as spending time on construction and painting. However, I don't live in an ideal world. I’m a part-time single dad with a demanding job and a limited budget, so I have to make choices about where I put my time, effort and money, and I’m focusing firmly on applying skill.
The kit I’ve chosen for this self-imposed craziness is Hasegawa’s 1/48 scale A7E Corsair II. I know the kit itself isn't up to modern standards. You’ll see below in the opening mini-review, that it has some old fashioned problems to overcome. That’s where the challenge comes in!
On the way I’m going to share my tips and techniques, my triumphs and tragedies, and experiment a little (and there’s been one near tragedy already).
I hope to learn from your experience and ideas too. After at least forty years of building model kits I have a way of doing things now — that could translate as great experience or stuck in my ways. I certainly know there’s more than one way to approach model making and I’m very interested in how you might tackle the problems and opportunities this kit throws up. All ideas thoughts and criticisms are welcome, except “Buy an after market part”!
Finally, just a word of warning about the speed of progress. Some er… patience may be required if you follow along, as I hope you will.
So, that’s the why. Now here’s the what…
Hasegawa’s A7E has been reviewed many times so I won’t go over old territory, except to point out some of the obvious highs and lows of the kit as they present opportunities or problems in the context of this blog. The highs are nice panel lines, some great detail and a relatively good price now. The lows are some really bad ejector pin marks, flash, soft detail in some places and a lack of ordinance. I’ve tried to capture some of the best and worst below. We’ll see how she goes together as I progress.
There are well defined panel lines and rivet detail that look like they will hold a pin wash well
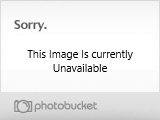
And some well detailed parts
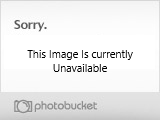
Along with detailed avionics bays
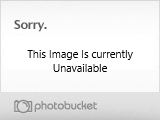
However, my kit came with a broken canopy part
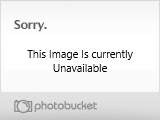
A scratched canopy
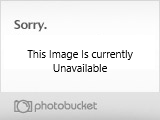
Some very awkward ejector pin marks

And a fair amount of flash
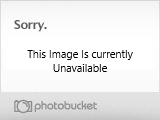
So, it is going to be fun and challenging build. More soon (including that near disaster)
All the best
Steve