So, most of know or have seen the Monogram 1/48 F-102A...typical of their mid-eighties releases; decent detail, pretty fair fit and fine, but raised panel lines. The Encore release gives us Monogram plastic, a decent selection of resin produced (as far as I know) by True Details and a couple of etched frets most likely from Eduard. Also included are Cartograph decals, but I've got an old set of Microscale markings that I'll be using instead.
>snipped from Scalemates project blog<
My second project on the way to a complete Century Series. Like all the older Monogram kits, this has pretty decent detail, but the surface detail is raised. Can't have that, so the first order of business is to re-scribe everything. To give me a nice 'roadmap' to follow, I first darken the area around the panel line with permanent marker, then sand back to the skin, removing the panel lines and most of the ink. Had this been molded in a dark plastic, I'd have just sprayed the whole thing in light gray or white primer and done the same thing.
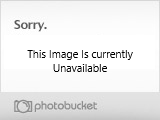
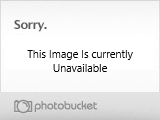
Scribing started on the wings. The mold changes from Case X to Case XX wings are a bit rough, requiring some filling. I've decided on using the resin control surface replacements supplied by Encore, though there's really no material improvement over the kit control surfaces, but the less-than-perfect mold revisions made it easier to replace than correct. For this project I'm using the MDC rivet punches rather than a sharp needed to replicate the airframe rivets, we'll see how it turns out. I'm of two minds on this bit of detail; the real jets had very clean surfaces with little or no rivet detail visible under the ADC Grey paint, but the addition of some visual interest breaks up the acres of featureless skin.

Neck deep into the scribing. It's a pain, but worth the effort. I'm using the UMM Universal Scriber as my weapon of choice, I've never found a better tool. Standard stainless steel templates and my trusty Dymo labeling tape. I think I need to purchase a wider variety of punch and die sets, doing circular panels is significantly easier with the correct size punched in the tape. Plus, compound or tight curves are less problematic. Also began applying a bit of paint. Model Claus brought a Grex Tritium pistol grip airbrush. All I can say is "wow".
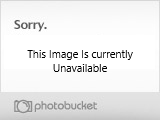
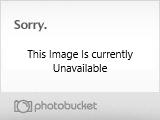