Hi,
I am desperate need of some advice on working with PE gun jackets.
I'm trying all the tricks I can find yet still no luck.
I've annealed the jacket, rolled it with progressively smaller rod, yet still cannot get it to form a perfect cylinder (at the ends it is more hexagonal) and cannot get the edges to meet at the bottom. Been at it all afternoon and it's now giving me a headache.
I'm working on Wnw's Rumpler and I am using the supplied tool to finish off the jacket.
What I am doing wrong and what witch craft is everyone else using?
I know that if all else fails I can use the simplified guns, but I would like to give them a proper go.
Thanks
Stephen
Start Here (for Beginners)
This forum is for younger modelers or people just starting out in the hobby.
This forum is for younger modelers or people just starting out in the hobby.
Hosted by Jim Starkweather
HELP! PE gun jackets
Posted: Saturday, July 08, 2017 - 07:57 PM UTC
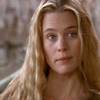
Jessie_C


Joined: September 03, 2009
KitMaker: 6,965 posts
AeroScale: 6,247 posts
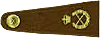
Posted: Saturday, July 08, 2017 - 11:35 PM UTC
What kind of surface are you rolling it on?
Posted: Saturday, July 08, 2017 - 11:54 PM UTC
A ceramic tile to get the shape. Then trying between my fingers for final shaping.
Another thing I'm finding difficult is keeping it all lined up. More than once I've had both ends go out of alignment.
Another thing I'm finding difficult is keeping it all lined up. More than once I've had both ends go out of alignment.
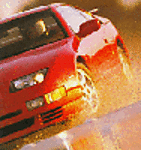
Scrodes

Joined: July 22, 2012
KitMaker: 771 posts
AeroScale: 763 posts
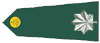
Posted: Saturday, July 08, 2017 - 11:58 PM UTC
Try using a rubber cutting mat - the cushion helps the barrel form better. Personally I prefer using drill bits to make the shape - there are so many various sizes. Roll to a size smaller than you actually want so when it springs back a bit you are where you want to be.
My $0.02
My $0.02
Posted: Sunday, July 09, 2017 - 12:20 AM UTC
Quoted Text
Try using a rubber cutting mat - the cushion helps the barrel form better. Personally I prefer using drill bits to make the shape - there are so many various sizes. Roll to a size smaller than you actually want so when it springs back a bit you are where you want to be.
My $0.02
I hadn't thought of that. Thanks. I'll give it a go tomorrow.
PE always seems to be my nemesis!
Posted: Monday, July 10, 2017 - 12:17 AM UTC
Tried again tonight and this is as good as I can get. The whole thing is completely bent out of shape and I don't think it's salvageable. I cannot work out what I'm doing wrong as I'm using every piece of advice and tutorial I can find.
Somehow I even managed to get a twist in the jacket and mangle the perforations.
Think I'll chalk this up to experience and move on. I hate PE!
Thanks to everyone who offered advice.
Somehow I even managed to get a twist in the jacket and mangle the perforations.
Think I'll chalk this up to experience and move on. I hate PE!
Thanks to everyone who offered advice.
Posted: Monday, July 10, 2017 - 12:59 AM UTC
Hi Stephen
Not a great result
- and I can't really see what went so wrong between your own preparation and the good advice which followed.
One way or another, it should have worked. I normally start rolling with a larger diameter to induce the curl and work steadily tighter - and if the metal's suitably softened, you've got scope to change your mind.
If you've got a drill-bit/rod etc. the correct diameter, I reckon you should still be able to bully that back into looking more presentable, but I can totally understand your disappointment.
All I can really advise is... try again. Especially while the experience is fresh in mind and you're a bit angry. Rather like being thrown by a horse (yes, I've been through that! LOL!). Grab some spare metal from the edge of an etched fret and try to roll it into a cylinder.
All the best
Rowan
Not a great result

One way or another, it should have worked. I normally start rolling with a larger diameter to induce the curl and work steadily tighter - and if the metal's suitably softened, you've got scope to change your mind.
If you've got a drill-bit/rod etc. the correct diameter, I reckon you should still be able to bully that back into looking more presentable, but I can totally understand your disappointment.
All I can really advise is... try again. Especially while the experience is fresh in mind and you're a bit angry. Rather like being thrown by a horse (yes, I've been through that! LOL!). Grab some spare metal from the edge of an etched fret and try to roll it into a cylinder.
All the best
Rowan

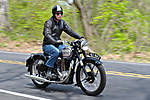
rdt1953

Joined: February 06, 2015
KitMaker: 1,098 posts
AeroScale: 900 posts
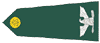
Posted: Monday, July 10, 2017 - 01:31 AM UTC
Try a glass plate - the surface is much flatter than ceramic tile.You may need to continually anneal between each step down to smaller dia rod as metals are prone to " work hardening" - the very act of forming can temper. As others have suggested start with large dia drill bits and work progressively down GENTLY- the rolling alone will form it - excessive pressure is not necessary and in fact can deform. If the ends do not align you may not be keeping the roller aligned axialy - that is always parallel to the edges of your workpiece. The fragile mesh center section may be stretching and causing problems as well.
If you know the finished outside diameter of your jackets and you have a rod or drill bit of that diameter you might try casting a female die around the bit .
Use Durhams water putty or plaster of Paris to make a trough like negative half cylinder that you can gently form the jacket into using a rod of the appropriate inside diameter. Hope this may be of some help - don't give up - you can do this !
Cheers - Richard
If you know the finished outside diameter of your jackets and you have a rod or drill bit of that diameter you might try casting a female die around the bit .
Use Durhams water putty or plaster of Paris to make a trough like negative half cylinder that you can gently form the jacket into using a rod of the appropriate inside diameter. Hope this may be of some help - don't give up - you can do this !
Cheers - Richard

Kevlar06

Joined: March 15, 2009
KitMaker: 3,670 posts
AeroScale: 833 posts

Posted: Monday, July 10, 2017 - 01:52 AM UTC
Quoted Text
Tried again tonight and this is as good as I can get. The whole thing is completely bent out of shape and I don't think it's salvageable. I cannot work out what I'm doing wrong as I'm using every piece of advice and tutorial I can find.
Somehow I even managed to get a twist in the jacket and mangle the perforations.
![]()
Think I'll chalk this up to experience and move on. I hate PE!
Thanks to everyone who offered advice.
I don't think you've annealed it enough to properly soften the brass for a start. Secondly, you need to use an artists rubber mat and a solid brass or steel rod in a smaller diameter than the jacket to do the forming. I find it useful to start at one edge of the jacket, bend that edge around the rod, and then start rolling from that edge. The "hexagonal end" in your photo is a dead giveaway that not enough annealing heat was applied-- how did you anneal it? I use a set of cross tipped tweezers or a forced to wave the brass jacket through the lowest flame setting on a Berne-o-magic butane torch, until the jacket turns from bright brass to a variegated blue-black color. Too much heat and you'll melt it-- too little heat and you get the result you're dealing with now. Here's what I'd do to try and resolve your problem-- flatten the jacket out on a hard surface as much as possible. You might need to use a small hammer to get it flat again-then re-anneal it, and try again.
VR, Russ

Kevlar06

Joined: March 15, 2009
KitMaker: 3,670 posts
AeroScale: 833 posts

Posted: Monday, July 10, 2017 - 05:53 AM UTC
Quoted Text
Quoted TextTried again tonight and this is as good as I can get. The whole thing is completely bent out of shape and I don't think it's salvageable. I cannot work out what I'm doing wrong as I'm using every piece of advice and tutorial I can find.
Somehow I even managed to get a twist in the jacket and mangle the perforations.
![]()
Think I'll chalk this up to experience and move on. I hate PE!
Thanks to everyone who offered advice.
I don't think you've annealed it enough to properly soften the brass for a start. Secondly, you need to use an artists rubber mat and a solid brass or steel rod in a smaller diameter than the jacket to do the forming. I find it useful to start at one edge of the jacket, bend that edge around the rod, and then start rolling from that edge. The "hexagonal end" in your photo is a dead giveaway that not enough annealing heat was applied-- how did you anneal it? I use a set of cross tipped tweezers or a forced to wave the brass jacket through the lowest flame setting on a Berne-o-magic butane torch, until the jacket turns from bright brass to a variegated blue-black color. Too much heat and you'll melt it-- too little heat and you get the result you're dealing with now. Here's what I'd do to try and resolve your problem-- flatten the jacket out on a hard surface as much as possible. You might need to use a small hammer to get it flat again-then re-anneal it, and try again.
VR, Russ
Sorry-- I meant to say "forceps" not "forced" in my last post. A good annealing job heats the PE uniformly, but be careful, once annealed it will be really soft, and will bend very easily. You can return the part to its original stiffness by heating slightly again after it's properly formed and dunking it quickly into ice water. But always be careful heating with a torch, fragile PE can melt quickly-- experiment with the sides of the runners the PE comes on till you get the hang of it.
VR, Russ
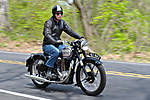
rdt1953

Joined: February 06, 2015
KitMaker: 1,098 posts
AeroScale: 900 posts
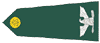
Posted: Monday, July 10, 2017 - 06:48 AM UTC
If I might add to Russ' excellent advise - when tempering ( re hardening ) any sheet stock ( flat ) by quenching always drop heated metal in coolant edgewise so both surfaces get quenched equally and at the same time - if you do not you run the risk of one side cooling more rapidly tha the other and warping will be the result.
Cheers - Richard
Cheers - Richard
Posted: Wednesday, July 12, 2017 - 02:28 AM UTC
Thanks again for the advice.
I've opened it back out and this is what I'm left with. Still needs a little more flattening out. Not sure how useable it will be, some of the perforations are seriously bent out of shape.
Going to give it one last shot and if it doesn't work I'm giving up. Just feel like I've wasted far too much time.
Maybe I could use it as war trophy in a diorama? Pinned to an RFC hanger wall?
I've opened it back out and this is what I'm left with. Still needs a little more flattening out. Not sure how useable it will be, some of the perforations are seriously bent out of shape.
Going to give it one last shot and if it doesn't work I'm giving up. Just feel like I've wasted far too much time.
Maybe I could use it as war trophy in a diorama? Pinned to an RFC hanger wall?
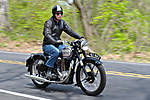
rdt1953

Joined: February 06, 2015
KitMaker: 1,098 posts
AeroScale: 900 posts
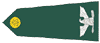
Posted: Wednesday, July 12, 2017 - 02:41 AM UTC
If you can clamp one end in a vise (pad the jaws )or onto the edge of the bench and grasp the other end with plain jaw pliers or pad the jaws and gently stretch you may see the mesh straighten a bit - easy does it -
good luck - don't quit - hobbies are fun , right ?
Rooting for you - Richard
good luck - don't quit - hobbies are fun , right ?
Rooting for you - Richard

Kevlar06

Joined: March 15, 2009
KitMaker: 3,670 posts
AeroScale: 833 posts

Posted: Wednesday, July 12, 2017 - 05:38 AM UTC
Quoted Text
If you can clamp one end in a vise (pad the jaws )or onto the edge of the bench and grasp the other end with plain jaw pliers or pad the jaws and gently stretch you may see the mesh straighten a bit - easy does it -
good luck - don't quit - hobbies are fun , right ?
Rooting for you - Richard
Stephen,
You might also try to flatten it with a hard metal plate and a small hammer, sandwiching it between a hard work surface and the metal plate. You might find it even straightens out a little while rolling. I sent you a PM regarding the use of a candle for a heat source, not ideal, but it can be done, it just needs more time to heat-- having said that, the process off annealing can be collective in nature, and the more you anneal something the weaker it can become-- so, as Richard said-- go easy with the rolling and tool work.
VR, Russ

Kevlar06

Joined: March 15, 2009
KitMaker: 3,670 posts
AeroScale: 833 posts

Posted: Thursday, July 13, 2017 - 05:16 AM UTC
Hey Stephen --sent you a PM, but you might look at the Master and Aber pre-rolled cooling jacket and barrels-- a more expensive option but at leas you don't have to fool with annealing.
VR, Russ
VR, Russ
Posted: Saturday, July 15, 2017 - 09:45 PM UTC
Thanks to everyone.
I'm going to have a play around with it and see how I get on.
In the meantime and to get this kit built to the standard I want, I've oderered Karaya's pre-formed jackets for the LMG08/15 and LMG14.
A small price to pay, but They'll save me a lot of trouble until I get the hang of it.
I can add some photos and a write up when they arrive.
I also got myself a butane burner/soldering iron tool over the weekend. Should help with annealing.
I'm going to have a play around with it and see how I get on.
In the meantime and to get this kit built to the standard I want, I've oderered Karaya's pre-formed jackets for the LMG08/15 and LMG14.
A small price to pay, but They'll save me a lot of trouble until I get the hang of it.
I can add some photos and a write up when they arrive.
I also got myself a butane burner/soldering iron tool over the weekend. Should help with annealing.
![]() |