Quoted Text
but happy AMS if you havent.... laughs demonically
AMS? Why whatever do you mean... grins, rolls blood red eyes and also laughing demoniacally
You are as twisted as I am

... If you are ever in Jersey we should have a beer
And no I did not have that site so thanks for that.
Work continues on the engine, slowly but surely. Needed to make the plates on top if the springs for the lifters. They are not flat but have a curled under edge with a dimple in the middle. I came up with this...
The 2nd to smallest punch on the Micro Mark set fits the top of the spring. To figure out what size bit to use to make the little rings I doubled the size of the wire (0.02) and the thickness of the lead foil (0.1). Take that off the size of the punch, .058 leaving .038. I went down a tiny bit to a #65 bit at .035 for some wiggle room.
In the standard ring making manner, wrap the wire around the bit shank and cut of the rings. Press the lead foil over the ring. Run a burnishing tool around the outside of the ring and make a dimple in the middle. This should capture the ring which is what you want. The next step will explain why the calculations. Turn the foil over and the shape of the rich should rest perfectly in the hole for the punch... ring side up. Now gently punch it out and, Bob's your uncle, lifter spring covers.
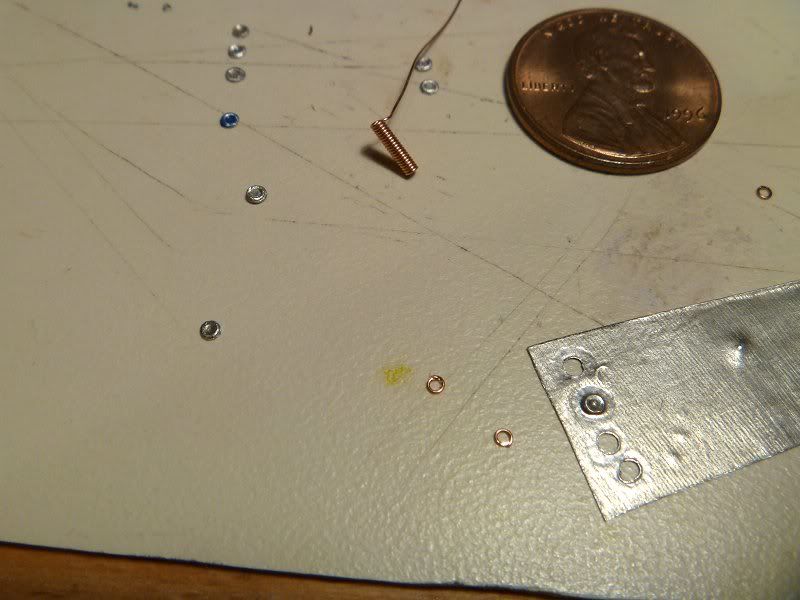
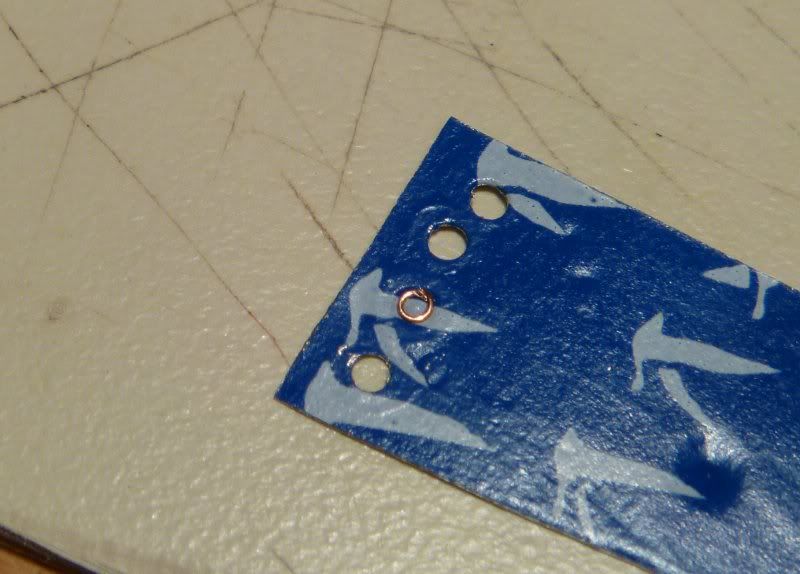
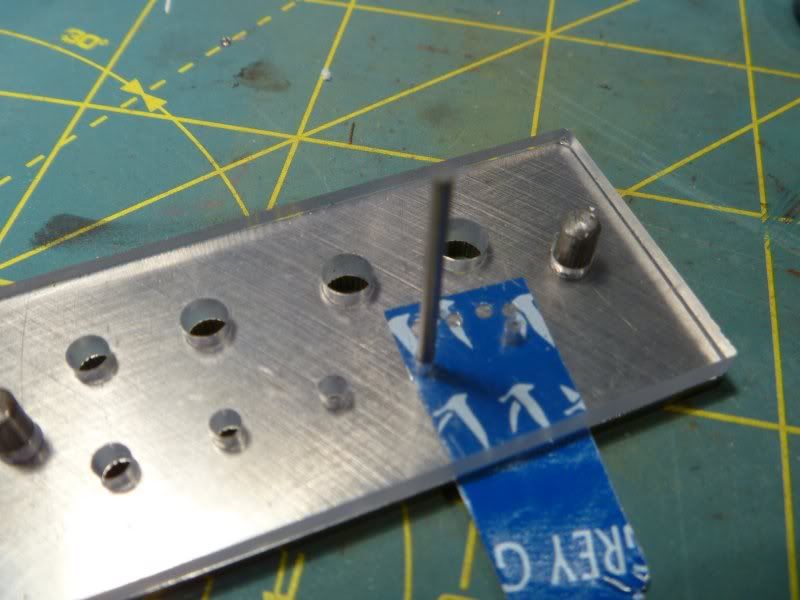
The nuts, such as they were, by the lifter were chiseled off and replaced with Tichy plastic bolts heads. I get these at a local model RR shop. The engine mount bolts were replaced with machined brass from Scale Hardware. The brass stuff is some of the most amazing stuff that add a great light bit of detail look. The engine is just dry fit at the moment waiting for paint.