Dry-fitting for fun! No...not really.
Because of this bird's unique shape, I haven't been in a rush to complete the cockpit, Propeller assemblies, or gun turrets. Regarding the latter two, I'm going to install them last no matter how much I have to modify them. I just can't see myself puttying, Scraping, and sanding without ruining them if they were in place. I don't need them to spin or rotate.
this is the bow shot with two insets.
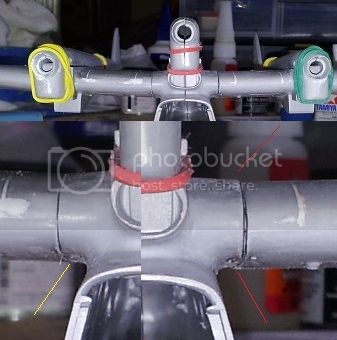
On the port wing, I'll have to expand the hole for one locator pin and pivot the forward edge upwards to get it into place. Note the red lines. On the starboard wing, I'll have to reduce the thickness of the inner wing so that it matches the wing root.
On this dorsal shot, you can see that all four corners of the wing roots are gonna need some kind of treatment.
At this time, I'm not sure where to add, and where to remove.
On this port view, you can see that at both front and rear edges of the wings, I have to decide what I'll keep and what I'll remove. Do I bring the wing up to the boom, or the boom down to the wing?
What scares me most, is that once I think the plane is ready for painting, my eyes will notice that the plane's (generally) square shape is twisted.
It's sort of opposite on the starboard side.
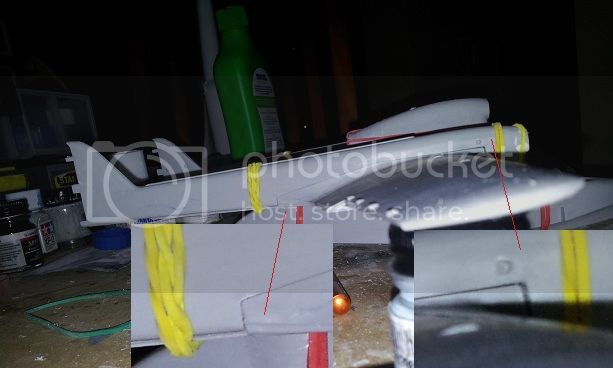
The portion of the lower wing that joins with the starboard boom is actually thinner than that of the port wing...challenges...challenges.
I really wasn't counting on things being this difficult. The last time I built a twin-boom aircraft was in the seventies. I think it was the 1/48 scale Monogram P-38. Back then I could build a plane in an afternoon. Heh...but I'd never even had a tube of putty.
Finally a 3/4 shot. On both dorsal and ventral sides of both booms are long skinny pieces {note yellow brackets} that are probably way-over scale in width. I'd like to replace them with something thinner without too much need for putty and sanding. I have lead and brass sheet available, but during cutting it would probably turn into curlicues. I have wire, too but being round, it would take filling, and like the sheet would be difficult to straighten perfectly. Their only benefits over sheet styrene is that they can take punishment while the filling and sanding is going on. Any ideas?
The red brackets just show more gaps or ledges to ponder and fix.
Thank you for reading!
And as usual, your critiques or helpful ideas are appreciated.
Gary
Edit: Typos