Gary,
wow!! Now we're in Metal Shop 101. Your decisions are sound, and the application proves it out that all will work. the offset washers glued into place is a most simple, yet highly effective solution to the angle problem.
Joel
World War II
Discuss WWII and the era directly before and after the war from 1935-1949.
Discuss WWII and the era directly before and after the war from 1935-1949.
Hosted by Rowan Baylis
B-29 Superfortress Jumbo King of the Show

Joel_W


Joined: December 04, 2010
KitMaker: 11,666 posts
AeroScale: 7,410 posts
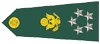
Posted: Tuesday, April 12, 2016 - 08:53 PM UTC
Posted: Wednesday, April 13, 2016 - 05:22 PM UTC
Wow Gary!
just, wow!


Posted: Thursday, April 14, 2016 - 07:13 AM UTC
Joel and Russell, thank you! Having some brass and a few simple tools handy are great when you need to find better strength than styrene will afford. Now that support is arranged, I can turn to dealing with those blisters. Once that is done, we can move onto buttoning her up.
Cheers,
Gaz
Cheers,
Gaz

KelticKnot

Joined: May 11, 2015
KitMaker: 768 posts
AeroScale: 656 posts
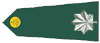
Posted: Thursday, April 14, 2016 - 02:57 PM UTC
I suppose any kit with etch or resin is technically "mixed media" but you've taken that term to a new level ! Re-engineering kits is fascinating work and as your washer solution shows its sometimes the simplest out of the box thinking that works best.
You're tantalisingly close to a complete fuselage, keep it up !
You're tantalisingly close to a complete fuselage, keep it up !
Posted: Friday, April 15, 2016 - 11:57 AM UTC
Hi Everyone,
Another hefty day of modelling just to get a few cubic centimeters done.
Thanks Paul! This is definitely a learn-as-I-go prospect.
After a week of ruminating on the best way to deal with making the waist blisters impervious to clumsiness and bad luck, I set myself to it today.
Because the kit has the extra parts to portray Enola Gay, I had no trouble coming up with the materials to make some large styrene washers. My shed provided a length of copper pipe.
That little red pipe cutter is no larger than my thumb, but will cut tubing nicely down to 3mm. Smaller than that, I need edge cutters and a file to get the cross-section back.
This stuff holds clear plastic well without fogging.
The only thing holding the blisters and their support in place is friction. If I press on one blister, the entire opposite side of the model is providing support.
This is an extreme close-up of the blister with a lot of back lighting.
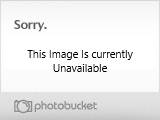
The blister itself is very reflective, so getting an image of the sighting device without back-light is virtually impossible.
So, another problem solved... again at the cost of interior detail. I will now let the blister assembly cure overnight. With any luck, the fuselage will be sealed up tomorrow.
Thanks for looking!
Gaz
Another hefty day of modelling just to get a few cubic centimeters done.
Thanks Paul! This is definitely a learn-as-I-go prospect.
After a week of ruminating on the best way to deal with making the waist blisters impervious to clumsiness and bad luck, I set myself to it today.
Because the kit has the extra parts to portray Enola Gay, I had no trouble coming up with the materials to make some large styrene washers. My shed provided a length of copper pipe.
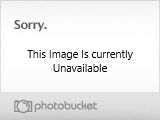
That little red pipe cutter is no larger than my thumb, but will cut tubing nicely down to 3mm. Smaller than that, I need edge cutters and a file to get the cross-section back.
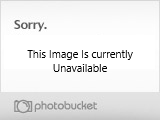
This stuff holds clear plastic well without fogging.
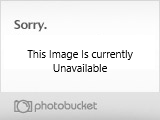
The only thing holding the blisters and their support in place is friction. If I press on one blister, the entire opposite side of the model is providing support.
This is an extreme close-up of the blister with a lot of back lighting.
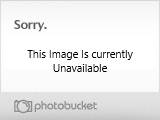
The blister itself is very reflective, so getting an image of the sighting device without back-light is virtually impossible.
So, another problem solved... again at the cost of interior detail. I will now let the blister assembly cure overnight. With any luck, the fuselage will be sealed up tomorrow.
Thanks for looking!
Gaz
Posted: Friday, April 15, 2016 - 02:42 PM UTC
That's still "WOW" from me, Gary

Posted: Friday, April 15, 2016 - 03:53 PM UTC
Russel,
Thanks!
Thanks!

Joel_W


Joined: December 04, 2010
KitMaker: 11,666 posts
AeroScale: 7,410 posts
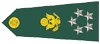
Posted: Friday, April 15, 2016 - 06:11 PM UTC
Gary,
Now you being an ex-Yank, it's plain as day that you've lost none of your Yankee ingenuity. What a great idea, and your fabrication is flawless. The end result is darn perfect.
I haven't used Micro Weld in more then 30 years. I've always assumed it's just 1st generation CCA glue, and most major brands would be far superior. Am I right or does it behave like Extra Thin with CCA properties?
Joel
Now you being an ex-Yank, it's plain as day that you've lost none of your Yankee ingenuity. What a great idea, and your fabrication is flawless. The end result is darn perfect.
I haven't used Micro Weld in more then 30 years. I've always assumed it's just 1st generation CCA glue, and most major brands would be far superior. Am I right or does it behave like Extra Thin with CCA properties?
Joel
Posted: Saturday, April 16, 2016 - 02:04 AM UTC
Hi Joel,
Thank you for liking my fix. It wasn't my original plan, but it seemed like the strongest option.
I don't know much about the earlier forms of CA or CCA. Being out of the hobby for so long, my glue knowledge has a gap between the time that Testors changed their toxic cement to the orange tube, citrus smelly stuff and literally, two years ago.
My main reason for purchasing it was that it doesn't craze clear parts and is stronger for that than white glue.
I tried it for main assemblies but the seams weren't as strong as those I could get using dissolved sprue. Despite it's weld name, I haven't got it to act that way. Perhaps it's because I'm using a paint brush instead of a flow-and-go.
But it is non-toxic, and while wet can be washed away with water. It's a nice middle-of-the-road cement, for me. I really dislike having to trust any joint to white glue.
Cheers,
Gaz
Thank you for liking my fix. It wasn't my original plan, but it seemed like the strongest option.
I don't know much about the earlier forms of CA or CCA. Being out of the hobby for so long, my glue knowledge has a gap between the time that Testors changed their toxic cement to the orange tube, citrus smelly stuff and literally, two years ago.
My main reason for purchasing it was that it doesn't craze clear parts and is stronger for that than white glue.
I tried it for main assemblies but the seams weren't as strong as those I could get using dissolved sprue. Despite it's weld name, I haven't got it to act that way. Perhaps it's because I'm using a paint brush instead of a flow-and-go.
But it is non-toxic, and while wet can be washed away with water. It's a nice middle-of-the-road cement, for me. I really dislike having to trust any joint to white glue.
Cheers,
Gaz
Posted: Saturday, April 16, 2016 - 09:19 AM UTC
Hi Everyone!
After years of sitting in the box...though still sealed in their plastic envelopes... the wings have warped a bit.
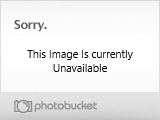
The colored arrows are there to hint at some subtle and some not so subtle warping.
So the question is: How do we fix this?
Hot water? No way! Every time I've tried the hot water technique, an entire kit ends up being hauled away with the trash.
The answer is:
Spars!
Made with square brass tubing and then soldered together in my usual sloppy fashion. Once I button up the fuselage I can reassemble the entire wing spar and wheel well assemblies and figure out the next step.
Next question: Is the carpet beige or gray?
The answer is: Yes!
Thank you for looking!
Gaz
After years of sitting in the box...though still sealed in their plastic envelopes... the wings have warped a bit.
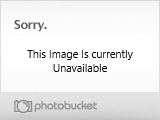
The colored arrows are there to hint at some subtle and some not so subtle warping.
So the question is: How do we fix this?
Hot water? No way! Every time I've tried the hot water technique, an entire kit ends up being hauled away with the trash.
The answer is:
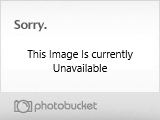
Spars!
Made with square brass tubing and then soldered together in my usual sloppy fashion. Once I button up the fuselage I can reassemble the entire wing spar and wheel well assemblies and figure out the next step.
Next question: Is the carpet beige or gray?
The answer is: Yes!
Thank you for looking!
Gaz

Joel_W


Joined: December 04, 2010
KitMaker: 11,666 posts
AeroScale: 7,410 posts
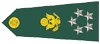
Posted: Sunday, April 17, 2016 - 03:40 AM UTC
Gary,
Looks don't count as no one will ever see those spars once the wings are closed up. The main thing is that they force the wings back into their proper shape when glued up.
Joel
Looks don't count as no one will ever see those spars once the wings are closed up. The main thing is that they force the wings back into their proper shape when glued up.
Joel

Kilo_Uniform

Joined: July 03, 2015
KitMaker: 280 posts
AeroScale: 141 posts
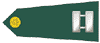
Posted: Sunday, April 17, 2016 - 10:12 AM UTC
Hi Gary,
Awesome work on the blisters - very ingenious.
I'm sure you will sort out the warped wings and, once done, 99.99% of the people won't even know they were warped (the only people who will know are the ones that read your build-log).
Regards,
Kobus
Awesome work on the blisters - very ingenious.
I'm sure you will sort out the warped wings and, once done, 99.99% of the people won't even know they were warped (the only people who will know are the ones that read your build-log).
Regards,
Kobus
Posted: Sunday, April 17, 2016 - 12:09 PM UTC
Joel and Kobus,
Thank you for your kind words. I've never gone to these lengths to make a kit more correct and sturdy. I hope to get past the mechanical aspects soon and move into dealing with the pretty stuff.
Gaz
Thank you for your kind words. I've never gone to these lengths to make a kit more correct and sturdy. I hope to get past the mechanical aspects soon and move into dealing with the pretty stuff.
Gaz
Posted: Sunday, April 17, 2016 - 02:45 PM UTC
Hi Gary
Very neat!
That metal spar would be ideal for Revell-Monogram's Ta 154 - every example I've seen suffered from a slightly warped wing.
All the best
Rowan
Very neat!

All the best
Rowan

Posted: Wednesday, April 20, 2016 - 12:16 PM UTC
Hi Everyone
A bit of an update today. I lost a lot of time looking for half of the B-29's hydraulically lowered tail skid. It looks like this IRL: (photo included for discussion only)

Anyway, the important thing is that I found it before the cat, the dogs, or the vacuum cleaner did! Because it's a two part assembly that has to be fitted at the same time as joining the fuselage halves, it's drying between the halves which are held together with tape at the mo.
Rowan, though tempted to build the TA-154 years ago, I've never gotten around to it. But no I know to buy more brass when I do. Thanks!
With the fuselage bound up with tape, I busied myself with a modification of one of the four sets of cooling louvres that just wouldn't let me let them slide. Here are some photos and thoughts:

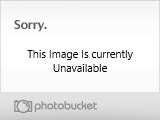
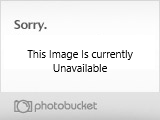
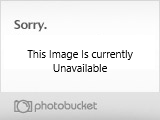
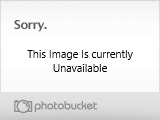
Thank you for looking!
P.S. If you have any useful knowledge about soda cans and scale modelling, I'd be very appreciative.
Gaz
P.P.S. I got the louvres totally wrong. Further study shows that they look nothing like what I've done. I'd like to see a mechanical drawing of them.
A bit of an update today. I lost a lot of time looking for half of the B-29's hydraulically lowered tail skid. It looks like this IRL: (photo included for discussion only)

Anyway, the important thing is that I found it before the cat, the dogs, or the vacuum cleaner did! Because it's a two part assembly that has to be fitted at the same time as joining the fuselage halves, it's drying between the halves which are held together with tape at the mo.
Rowan, though tempted to build the TA-154 years ago, I've never gotten around to it. But no I know to buy more brass when I do. Thanks!
With the fuselage bound up with tape, I busied myself with a modification of one of the four sets of cooling louvres that just wouldn't let me let them slide. Here are some photos and thoughts:

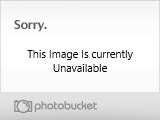
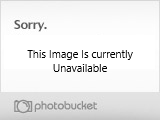
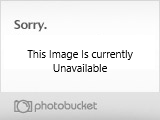
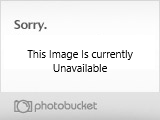
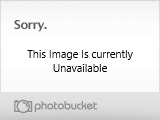
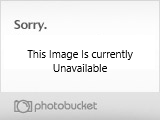
Thank you for looking!
P.S. If you have any useful knowledge about soda cans and scale modelling, I'd be very appreciative.
Gaz
P.P.S. I got the louvres totally wrong. Further study shows that they look nothing like what I've done. I'd like to see a mechanical drawing of them.
Posted: Wednesday, April 20, 2016 - 04:04 PM UTC
Gaz, yes you need to fix the cowl flaps! If you find you are missing some small parts, let me know. I have plenty of spares I could send you!

Joel_W


Joined: December 04, 2010
KitMaker: 11,666 posts
AeroScale: 7,410 posts
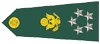
Posted: Wednesday, April 20, 2016 - 09:37 PM UTC
Gary,
No sense chiming in on the cowl flaps. I'm quite sure you'll come up with new ones that are a lot closer to the real ones.
I'm just super impressed with the foiling on that engine cowl. Great job.
Joel
No sense chiming in on the cowl flaps. I'm quite sure you'll come up with new ones that are a lot closer to the real ones.
I'm just super impressed with the foiling on that engine cowl. Great job.
Joel
Posted: Thursday, April 21, 2016 - 03:22 AM UTC
Quoted Text
Gary,
No sense chiming in on the cowl flaps. I'm quite sure you'll come up with new ones that are a lot closer to the real ones.
I'm just super impressed with the foiling on that engine cowl. Great job.
Joel
Gary, it it was me, I would re-do the cowl flaps out of thin sheet styrene. Better yet, would it be possible to cut them out of a thin aluminum sheet? That way you wouldn't have to foil them, just attach them to the after cowlings.
Posted: Thursday, April 21, 2016 - 06:31 AM UTC
Brian, I'm trying to find some decent drawings of the original article, because there appears to be a second layer behind the outer flaps. Whether the inner layer is full sized like the outer layer I can't tell. Finding useful photos isn't proving easy.
I read up on gluing aluminium to plastic last night, and it looks like it is prone to detaching from a lot of glues at the least provocation. Basically I want to go the sheet aluminium route, I just wanna make sure that I can attach it firmly and preeminently.
Again, I find myself on the brink of a new learning experience.
Gaz
I read up on gluing aluminium to plastic last night, and it looks like it is prone to detaching from a lot of glues at the least provocation. Basically I want to go the sheet aluminium route, I just wanna make sure that I can attach it firmly and preeminently.
Again, I find myself on the brink of a new learning experience.
Gaz
Posted: Thursday, April 21, 2016 - 05:19 PM UTC
Quoted Text
Brian, I'm trying to find some decent drawings of the original article, because there appears to be a second layer behind the outer flaps. Whether the inner layer is full sized like the outer layer I can't tell. Finding useful photos isn't proving easy.
I read up on gluing aluminium to plastic last night, and it looks like it is prone to detaching from a lot of glues at the least provocation. Basically I want to go the sheet aluminium route, I just wanna make sure that I can attach it firmly and preeminently.
Again, I find myself on the brink of a new learning experience.
Gaz
I looked to see if Eduard's extensive brass sets for the 29 included cowl flaps, like on the 17, but no. I would tend to agree that thin but stiff aluminum sheet is the way to go here. But yeah, cutting it out is the challenge. If you had a machine shop friend somewhere with a CNC cutter that might be the way to go. Certainly the technology exists.
Your build is paying far more attention to structural/design deficiencies in the original kit than my build did. I think this is going to turn out to be an awesome model.

mattemoore

Joined: November 10, 2006
KitMaker: 10 posts
AeroScale: 2 posts
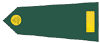
Posted: Thursday, April 21, 2016 - 06:14 PM UTC
Hi, I've been lurking here for a while and wanted to say how much I'm enjoying your build. Thank you!
Based on images I've seen of the flaps open during repairs I think every other flap has recessed extensions on either side that tuck under the flaps next to it.
Here is a link to the image I'm talking about.
https://s-media-cache-ak0.pinimg.com/736x/f4/84/cc/f484cc1521a73c41f4eb18b9b0e69710.jpg
Thank you again for your very entertaining and informative blog.
-Matt
Based on images I've seen of the flaps open during repairs I think every other flap has recessed extensions on either side that tuck under the flaps next to it.
Here is a link to the image I'm talking about.
https://s-media-cache-ak0.pinimg.com/736x/f4/84/cc/f484cc1521a73c41f4eb18b9b0e69710.jpg
Thank you again for your very entertaining and informative blog.
-Matt

berndm

Joined: March 26, 2014
KitMaker: 844 posts
AeroScale: 630 posts
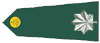
Posted: Thursday, April 21, 2016 - 10:17 PM UTC
Looks like Aeroscale is the home of the four engined bombers. Awesome build.
Posted: Friday, April 22, 2016 - 07:15 AM UTC
Guys,
Thank you for your replies.
Brian, it would be nice to have a friend with a CNC machine. I'm not unarmed when it comes to working metal. I've dabbled in it for a while, but am uncertain about getting the required shape from a piece that is 6.8mm by 7mm plus. Despite it's simple construction the little flap has a complex shape. Even more annoying is that the flaps are different sizes. My styene-and-soda can experiment is still curing, 18-hours later. I'm using a product that has enabled me to re-attach car weather stripping as well as enabling me to cement angle PVC to a decorative wood strip. It bears the name Soudal Fix All.
Matt, thank you for your compliment and the photo reference. Honestly, it never occurred to me that every other flap might have an extension. I looked at that same picture in a smaller size yesterday but couldn't really decipher what I was looking at. I appreciate your insight!
Bernd, thank you! If this bomber turns out as well as your latest FW's, I'll be very pleased.
Gaz
Thank you for your replies.
Brian, it would be nice to have a friend with a CNC machine. I'm not unarmed when it comes to working metal. I've dabbled in it for a while, but am uncertain about getting the required shape from a piece that is 6.8mm by 7mm plus. Despite it's simple construction the little flap has a complex shape. Even more annoying is that the flaps are different sizes. My styene-and-soda can experiment is still curing, 18-hours later. I'm using a product that has enabled me to re-attach car weather stripping as well as enabling me to cement angle PVC to a decorative wood strip. It bears the name Soudal Fix All.
Matt, thank you for your compliment and the photo reference. Honestly, it never occurred to me that every other flap might have an extension. I looked at that same picture in a smaller size yesterday but couldn't really decipher what I was looking at. I appreciate your insight!
Bernd, thank you! If this bomber turns out as well as your latest FW's, I'll be very pleased.
Gaz
Posted: Friday, April 22, 2016 - 11:42 AM UTC
Hi Everyone!
While I'm waiting for some glue to cure, I decided to explore another cooling flap option. To have them closed. Many of the pictures of the B-29 show the louvres in the closed position. Unfortunately for me, I think most radials look coolest with the cooling flaps open. Sadly, there is no detail to put behind open flaps, and no good photos to help a guy fill that space.
Never let it be said that I am afraid to take the path of the least resistance.
With file and sandpaper I brought the cooling flaps into their aerodynamically cleanest state. I had to rescribe the divisions between them, but that was no big deal.
I look forward to your opinions.
BTW...the last rays of the setting sun are partially obscured by clouds and a local tree.
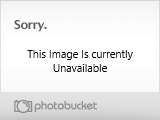
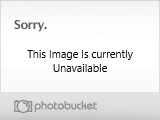
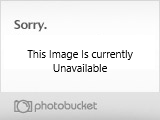
Heh...a golden ray of sunlight slipped through on this one!
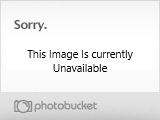
Thanks for looking.
Gaz
While I'm waiting for some glue to cure, I decided to explore another cooling flap option. To have them closed. Many of the pictures of the B-29 show the louvres in the closed position. Unfortunately for me, I think most radials look coolest with the cooling flaps open. Sadly, there is no detail to put behind open flaps, and no good photos to help a guy fill that space.
Never let it be said that I am afraid to take the path of the least resistance.
With file and sandpaper I brought the cooling flaps into their aerodynamically cleanest state. I had to rescribe the divisions between them, but that was no big deal.
I look forward to your opinions.
BTW...the last rays of the setting sun are partially obscured by clouds and a local tree.
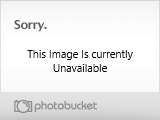
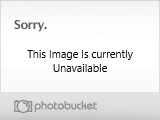
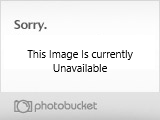
Heh...a golden ray of sunlight slipped through on this one!
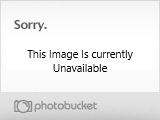
Thanks for looking.
Gaz
Posted: Friday, April 22, 2016 - 06:04 PM UTC
Yes! Closed flaps is the way to go IMO.
Re the props, there's a bit of glop on one of the blades to be fixed, and I would definitely recommend adding the yellow stenciling and Ham-Standard logos. But I'm sure you were planning this anyway.
This build is coming along beautifully, Gary. I know of no other modeler who has the stones to attempt aluminum-foiling this beast. You are doing a magnificent job on this.
Re the props, there's a bit of glop on one of the blades to be fixed, and I would definitely recommend adding the yellow stenciling and Ham-Standard logos. But I'm sure you were planning this anyway.
This build is coming along beautifully, Gary. I know of no other modeler who has the stones to attempt aluminum-foiling this beast. You are doing a magnificent job on this.
![]() |