Here is my set up....I shoot with a 20lb Co2 tank. Psi is set between 10-13 psi. Anything more and I run into problems with the paint drying before it hits the model which is akin to non-skid texture which isn't good on anything but a tank..

Very rarely do I ever have to increase this. I cut all my paints with lacquer thinner, Tamiya acrylics as well. I have 5 dedicated brushes that are used for a specific purpose in mind. The bottom two brushes are Iwata revolutions. The one on the left is for metallic only. The one on the bottom right is for acrylics and future. I cut my acrylics, other than Tamiya with Windex and they shoot well. I don't have a ratio, it is just something that I have come to be able to eyeball anymore. Top left is an Iwata HP-CH which I use for 90% of my work. Top right is an Iwata Custom Micron B which I use for extremely tight pattern work...think 1/72 or smaller German squiggle pattern camo. And last but not least in the middle looking like a bong of some sort is a Harder and Steenbeck Infinity. The funky looking tripod thing is its stand. I use this one also for tight pattern and detail work. I have all my brushed equipped with quick disconnects so I can change from one to the next easily. I used to have a 5 valve manifold, but it was constantly leaking and counter productive when I thought about it. All my brushes had the QD's on them, so I didn't really need the manifold. Something else I do with my brushes is seal the threads on the head assemblies with bees-wax. This ensures I always have a good seal and good airflow. When I'm done shooting for the day, the brushes get a thorough cleaning and a spritz of WD-40 in their paint cups then a couple pulls on the trigger to run it through. This helps keep the needles free from sticking should any paint residue still remain inside...It's important to remember to blast the WD-40 out though before you paint next or the first shot will be really glossy..

I've done it a few times. A couple drops of lacquer thinner cleans it out and I'm ready to paint.....
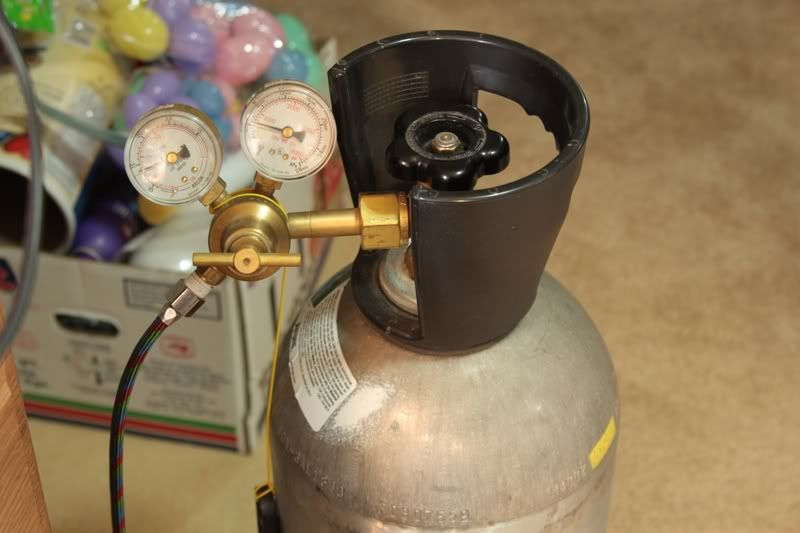
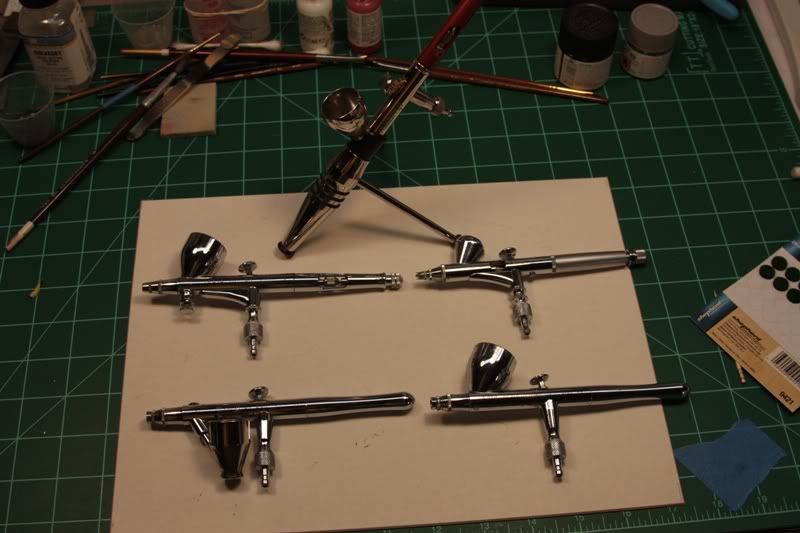
I used to run a compressor and had many of the same problems you had Bob. One of the biggest was the pressure drop, and the accumulation of moisture...I was living in the south at the time. I can't count how many paint jobs I had ruined because of that. Moisture traps didn't last long with the amount of water that was being produced. Once I made the switch to Co2 I never looked back. Initial set up was a little steep at around $200 and refills run just shy of $30, but I only have to have that done maybe 3 times a year. 1 for 1 exchange and no hydro testing every 5 years. No moving parts either...and it is whisper quiet. All fittings at the Co2 tank are wrapped with Teflon tape to ensure good tight seals.
Looking at your set up, I would suggest adding an additional inline water trap as close to the handle as you can. Paasche makes one that slips onto the line. I used to run one of these on my old VL brush. Even with the one coming out of the cylinder, moisture will accumulate in the hose before it hits your brush. Think of it as added insurance.
Sorry to get off topic, but I hope this helps. "Q"
