Gary
I'm pretty sure it wouldn't effect it at all but I would test it on a small piece of the exact clear plastic you are using. You know the old story about Murphy: What ever can go wrong, will go wrong. I've used Milliput a lot and never had any problems with crazing clear plastic but in this case, take no chances or prisoners without testing - just way to much work before hand.
Peter
World War II
Discuss WWII and the era directly before and after the war from 1935-1949.
Discuss WWII and the era directly before and after the war from 1935-1949.
Hosted by Rowan Baylis
B-29 Superfortress Jumbo King of the Show
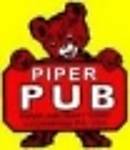
Peterpools

Joined: June 08, 2013
KitMaker: 197 posts
AeroScale: 193 posts
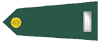
Posted: Wednesday, August 03, 2016 - 01:41 AM UTC
Posted: Wednesday, August 03, 2016 - 02:03 AM UTC
Thank you, Peter. Now I have a couple of methods I can test before going full tilt.
The model is so huge that almost any fault can be hidden just by the fact that to get all four corners of the bird in one shot you have to be a fair distance away. But I want interest areas like the canopy to be worthy of close scrutiny.
Gaz
The model is so huge that almost any fault can be hidden just by the fact that to get all four corners of the bird in one shot you have to be a fair distance away. But I want interest areas like the canopy to be worthy of close scrutiny.
Gaz
Posted: Wednesday, August 03, 2016 - 02:16 AM UTC
Quoted Text
Gary,
I've used Milliput a few times, and worked from a worm shape using a wet finger, you can smooth it out, same for Vallejo white putty. I would still mask out the area to keep it from attaching or attacking the canopy.
The big difference from my point of view, is that the Milliput will take hours to cure while the Vallejo acrylic putty will take just 5-10 to completely cure, so you can complete one panel then move on to the next one.
Joel
Joel,
Thank you. I understand what you are saying. Since this build seems to find ways to extend itself (Original finish line was expected to be this past May), I've settled into a slower expectation of completion. Waiting for Milliput to dry overnight is offset by the fact that it doesn't shrink at all. Perhaps Brian will be finished before me.
Masking is a serious weak point for me. I either have to cut a zillion tiny pieces and spend ages covering an area or expect that my unsteady hands will score the clear should I dare to touch it with a blade. So, I have to learn even more patience.
Best Wishes,
Gaz

Joel_W


Joined: December 04, 2010
KitMaker: 11,666 posts
AeroScale: 7,410 posts
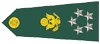
Posted: Wednesday, August 03, 2016 - 04:58 AM UTC
Quoted Text
Quoted TextGary,
I've used Milliput a few times, and worked from a worm shape using a wet finger, you can smooth it out, same for Vallejo white putty. I would still mask out the area to keep it from attaching or attacking the canopy.
The big difference from my point of view, is that the Milliput will take hours to cure while the Vallejo acrylic putty will take just 5-10 to completely cure, so you can complete one panel then move on to the next one.
Joel
Joel,
Thank you. I understand what you are saying. Since this build seems to find ways to extend itself (Original finish line was expected to be this past May), I've settled into a slower expectation of completion. Waiting for Milliput to dry overnight is offset by the fact that it doesn't shrink at all. Perhaps Brian will be finished before me.
Masking is a serious weak point for me. I either have to cut a zillion tiny pieces and spend ages covering an area or expect that my unsteady hands will score the clear should I dare to touch it with a blade. So, I have to learn even more patience.
Best Wishes,
Gaz
Gary,
I'm legally blind in the left eye, so I have almost no depth of field close up. I can't tell you how many times I touch the wrong spot with a paint brush, or with the brush from Tamiya Extra Thin. So believe me, I feel your pain and frustration. Just ask Pete how many times I've complained about screwing up because of my crappy eyesight.
The gasket in scale will be very small, and they don't look all that uniform, which is a good thing. Again, that's another reason why a worm of Milliput may be making it all that much harder. The lip created by the aluminum frame over the clear plastic is a really good sharp hard edge.
Here's how I would approach it. A piece of Tamiya tape over one pane at a time, use toothpick to scribe that demarcation line. Now remove the tape. Slowly using a new sharp blade cut out the mask following the line. You'll be left with a slightly smaller mask then the open dimensions of the pane. label the mask so you know where it goes.
When you're ready to do some of the panes, replace it, then apply a little Vallejo White Acrylic putty. Whipe smooth at a 45 degree angle, then remove the tape. You're done. If you have a slight glitch, just run a sharp toothpick along the edge of the gasket to clean it up. You can't do that with Milliput but you can do it with the Vallejo Acrylic putty.
Joel
Posted: Wednesday, August 03, 2016 - 05:28 AM UTC
Joel,
Thank you for expanding on your thoughts. I can see the sense of trying it this way. The masking tip will be very helpful! Heh...I just finished masking a 109 and see that I could have saved some time and effort that way.
Gaz
Thank you for expanding on your thoughts. I can see the sense of trying it this way. The masking tip will be very helpful! Heh...I just finished masking a 109 and see that I could have saved some time and effort that way.
Gaz
Posted: Wednesday, August 03, 2016 - 05:56 AM UTC
Gaz, what's the plan here? Machining the whole framework out of metal?! Any thought to working with the Sqdn. vacuform parts, which are the right shape?
Posted: Wednesday, August 03, 2016 - 07:08 AM UTC
Brian,
I have the vac form canopy and it is trimmed down to size. The main problem is between my hands, the foil, and the shape of the framing. I can't get good enough results because I can't cut a small enough curve. The angles all come out sharp and rough looking. So, I hafta go another way.
Gaz
I have the vac form canopy and it is trimmed down to size. The main problem is between my hands, the foil, and the shape of the framing. I can't get good enough results because I can't cut a small enough curve. The angles all come out sharp and rough looking. So, I hafta go another way.
Gaz
Posted: Thursday, August 04, 2016 - 06:48 AM UTC
Quoted Text
Brian,
I have the vac form canopy and it is trimmed down to size. The main problem is between my hands, the foil, and the shape of the framing. I can't get good enough results because I can't cut a small enough curve. The angles all come out sharp and rough looking. So, I hafta go another way.
Gaz
I mean, as I see it you got three levels here. First is the border around the main glass panels in the cockpit canopy. Most of those are gently rounded. Admittedly, I know nothing about foiling, but if you could do those engine access curves on the nacelles I certainly feel that you could mask off the window interiors on the vacuform canopy and then maybe use metallizer or paint or something? I know you used different materials with one of the turret bases, and I guess I'm suggesting that for this.
So far as the gaskets go, that's level II. When I masked off the canopy on my B-29 kit I simply included the space for the gaskets as exposed spray area for the olive drab paint. On your aircraft, however, as we see from the Enola Gay picture, the gaskets would be grey. Why not keep it that way? I would probably want to fiddle around with something like forms cut from the kabuki tape that I could make in the shape of the gaskets and apply on to the vacuform form canopy, after having sprayed the tape some kind of medium gray like the picture shows.
Of course the third and lowest level is the glass itself. But for what you want to do, I think simply covering up the clear windowpanes with kabuki tape and then painting the frames, and applying the gaskets third might be the best way to go.
I can tell you from my own build of this kit using the vacuum form canopy that this is one of the most tedious parts of the entire job. All the more so because it's the first place anybody is going to look at the finished kit.
Posted: Thursday, August 04, 2016 - 11:03 AM UTC
Brian,
I appreciate tout post and your thoughts. They do make sense, I assure you. I'm saving painting the framing as my final "I've-had-enough" option.
Foil only follows curves when the curves are there beforehand. The nacelle access hatches are the same .3mm thick aluminum flashing I am one planning on using for the greenhouse glazing. They were shaped with scissors and files before being glued to the nacelles.
Just today I've had other thoughts about how to go about it. I've got a bad case of tinkering in regards to this area, so will do my best to try to find a way to get past my physical failings.
Gaz
I appreciate tout post and your thoughts. They do make sense, I assure you. I'm saving painting the framing as my final "I've-had-enough" option.
Foil only follows curves when the curves are there beforehand. The nacelle access hatches are the same .3mm thick aluminum flashing I am one planning on using for the greenhouse glazing. They were shaped with scissors and files before being glued to the nacelles.
Just today I've had other thoughts about how to go about it. I've got a bad case of tinkering in regards to this area, so will do my best to try to find a way to get past my physical failings.
Gaz
Posted: Thursday, August 04, 2016 - 02:29 PM UTC
Quoted Text
Brian,
I appreciate tout post and your thoughts. They do make sense, I assure you. I'm saving painting the framing as my final "I've-had-enough" option.
Foil only follows curves when the curves are there beforehand. The nacelle access hatches are the same .3mm thick aluminum flashing I am one planning on using for the greenhouse glazing. They were shaped with scissors and files before being glued to the nacelles.
Just today I've had other thoughts about how to go about it. I've got a bad case of tinkering in regards to this area, so will do my best to try to find a way to get past my physical failings.
Gaz
I'll watch with great interest. You're soooooooooooo far beyond "just building a model airplane" at this point.


Twentecable

Joined: September 13, 2003
KitMaker: 339 posts
AeroScale: 244 posts
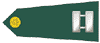
Posted: Monday, August 08, 2016 - 09:49 PM UTC
Gary I am curious how your metal canopy will work out. This is incredible just how many time can you afford to put in this models???
GR TC
GR TC
Posted: Monday, August 08, 2016 - 11:15 PM UTC
Hi Lars!
If we think of things in terms of only what we devote to them and not of what they give, or will give to us, I think very few projects would ever get finished.
At this moment, this part of the plane, while giving some frustrations is also providing me at chance to learn a bit of metal-shaping skills.
I have two campaign models in the works when I need a break, as well as other duties to attend. This makes it easier not to dwell on frustration.
In the end, I can look forward to a shining example of my handiwork in the shape of an elegant yet powerful warbird. So, I try to think in terms of reward as much as possible, and less of commerment.
Bw,
GS
If we think of things in terms of only what we devote to them and not of what they give, or will give to us, I think very few projects would ever get finished.
At this moment, this part of the plane, while giving some frustrations is also providing me at chance to learn a bit of metal-shaping skills.
I have two campaign models in the works when I need a break, as well as other duties to attend. This makes it easier not to dwell on frustration.
In the end, I can look forward to a shining example of my handiwork in the shape of an elegant yet powerful warbird. So, I try to think in terms of reward as much as possible, and less of commerment.
Bw,
GS
Posted: Thursday, August 11, 2016 - 01:47 PM UTC
Hi Everyone!
Once again, the program is up for a change.

This means I need to learn another new skill. Metal shaping. I want to be one of those wizards who can turn a sheet of metal into dang-near anything.





I know, I know. It's not really an update. More like announcing that there is yet another steep hill to climb before I reach the destination. Still....
Thanks for looking!
Gaz
Once again, the program is up for a change.

This means I need to learn another new skill. Metal shaping. I want to be one of those wizards who can turn a sheet of metal into dang-near anything.







I know, I know. It's not really an update. More like announcing that there is yet another steep hill to climb before I reach the destination. Still....
Thanks for looking!
Gaz

KelticKnot

Joined: May 11, 2015
KitMaker: 768 posts
AeroScale: 656 posts
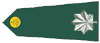
Posted: Thursday, August 11, 2016 - 03:56 PM UTC
Wow ! That's a radical approach to the problem.
You'll soon be custom building entire models from aluminium.
Aluminipples
You'll soon be custom building entire models from aluminium.
Aluminipples


Joel_W


Joined: December 04, 2010
KitMaker: 11,666 posts
AeroScale: 7,410 posts
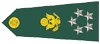
Posted: Thursday, August 11, 2016 - 07:45 PM UTC
Gary,
You've taken the Aluminum foiling process to unheard of levels. I don't think I've ever heard or seen anyone fashion parts from Aluminum other then turning them on a lath.
I'm really looking forward to your next update.
Joel
You've taken the Aluminum foiling process to unheard of levels. I don't think I've ever heard or seen anyone fashion parts from Aluminum other then turning them on a lath.
I'm really looking forward to your next update.
Joel
Posted: Friday, August 12, 2016 - 01:48 AM UTC
Paul,
Thanks for your reply. I don't know about whole planes. On Antiques Roadshow, I saw some bloke who made a Spitfire in about 1/32 scale from stainless steel years ago that they valued at 5,000 pounds. His was sculpted and polished and very fine looking.
Aluminum on the other hand oxidizes so rapidly that attaching it to anything is problematic if not using something like rivets.
Joel,
Glad to hear from you! I've been wanting to learn metal shaping for a few years now, but my original project was beyond my skills, or what I could learn quickly enough for my mindset. It got shelved, and consquently I have plenty of brass sheet around. I just hope I can master it well enough to satisfy me on this big bird.
Gaz
Thanks for your reply. I don't know about whole planes. On Antiques Roadshow, I saw some bloke who made a Spitfire in about 1/32 scale from stainless steel years ago that they valued at 5,000 pounds. His was sculpted and polished and very fine looking.
Aluminum on the other hand oxidizes so rapidly that attaching it to anything is problematic if not using something like rivets.
Joel,
Glad to hear from you! I've been wanting to learn metal shaping for a few years now, but my original project was beyond my skills, or what I could learn quickly enough for my mindset. It got shelved, and consquently I have plenty of brass sheet around. I just hope I can master it well enough to satisfy me on this big bird.
Gaz
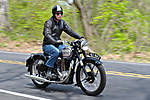
rdt1953

Joined: February 06, 2015
KitMaker: 1,098 posts
AeroScale: 900 posts
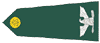
Posted: Friday, August 12, 2016 - 04:53 AM UTC
Gary - I've been watching your progress with admiration - thanks to you my ideas for my next effort have been derailed by visions of a foil covered project. A couple of thoughts on your greenhouse frame dilemma . Have you considered making a large scale expansion of the frame and having the framework photo etched ? If you went this route you likely would have to create dies - perhaps cast from the original canopy- of some material . Sounds laborious/ costly but you don't seem to shy away from effort so perhaps this may be a possibility.
If you have to resort to paint it is obvious to me that a person with your skills could create masks on the bench with the proper radiused corners- here again an expansion would be helpful - to be applied to the canopy after cutting.
So there - I've given you some more ingredients to throw in the stew pot - hope I haven't spoiled the broth. Keep it coming as I am enjoying your work very much !
Cheers ! Richard
If you have to resort to paint it is obvious to me that a person with your skills could create masks on the bench with the proper radiused corners- here again an expansion would be helpful - to be applied to the canopy after cutting.
So there - I've given you some more ingredients to throw in the stew pot - hope I haven't spoiled the broth. Keep it coming as I am enjoying your work very much !
Cheers ! Richard
Posted: Friday, August 12, 2016 - 09:33 AM UTC
Richard,
Thank you for your kind words and suggestions. I'd be interested to know about your foil covered aspiration.
I haven't even thought about PE. Do they even make aluminum PE? It just never occurred to me. I don't mind a little PE, but I've yet to buy any massive aftermarket sets of it. I'll keep an open mind should my current attempt prove impossible.
Though painting is my last option, I would really hate to have to bow to it. Once bitten by the aluminum bug it's hard to settle for less. Especially in an area that draws interest.
Best wishes,
Gaz
Thank you for your kind words and suggestions. I'd be interested to know about your foil covered aspiration.
I haven't even thought about PE. Do they even make aluminum PE? It just never occurred to me. I don't mind a little PE, but I've yet to buy any massive aftermarket sets of it. I'll keep an open mind should my current attempt prove impossible.
Though painting is my last option, I would really hate to have to bow to it. Once bitten by the aluminum bug it's hard to settle for less. Especially in an area that draws interest.
Best wishes,
Gaz

Joel_W


Joined: December 04, 2010
KitMaker: 11,666 posts
AeroScale: 7,410 posts
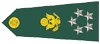
Posted: Friday, August 12, 2016 - 09:44 PM UTC
Gary,
While I have absolutely no skill set in Aluminum modeling, I've seen the work of masters like Dr. Park, who literally has built a few Corsairs and P-51s from Aluminum. And I'm talking engines, flying surfaces, the works. Perhaps visiting his site would give you some ideas and or direction. Sure can't hurt.
builders like me are just trying to come up with workable ideas, that may or may not work.
As a workable option, have you considered seeing if someone like Mal can make masks for the cockpit glass. Then you could use a Metalizer type paint for the framing. that would let you refocus your efforts to foiling.
Joel
While I have absolutely no skill set in Aluminum modeling, I've seen the work of masters like Dr. Park, who literally has built a few Corsairs and P-51s from Aluminum. And I'm talking engines, flying surfaces, the works. Perhaps visiting his site would give you some ideas and or direction. Sure can't hurt.
builders like me are just trying to come up with workable ideas, that may or may not work.
As a workable option, have you considered seeing if someone like Mal can make masks for the cockpit glass. Then you could use a Metalizer type paint for the framing. that would let you refocus your efforts to foiling.
Joel
Posted: Saturday, August 13, 2016 - 02:47 AM UTC
Joel,
Thank you! Your pointer to Dr. Park brought me some very much needed information.
You see, yesterday I almost had the shape I wanted when a crack developed in the bombardier's nose glazing area. This wasn't even in the area I was hammering, but it immediately turned that piece of aluminum into garbage. My suspect for the problem is improper annealing.
Some metals turn cherry red signifying that they are annealed properly. However, before turning red, aluminum will melt. I've melted a few pieces already. This was a missing piece of the puzzle for me. Most metal working sites work with materials much thicker than mine, because most metal smiths on line are making practical or automotive stuff. However, Dr. Park is using the same roof flashing as me!
Fortunately, Dr. Park has written a practical method on how to ensure your aluminum is properly annealed by the simple expedient of burning or heating away marks made with a red Sharpie.
I will definitely invest more time on learning from Dr. Park.
So, once again, you've improved my modelling knowledge, my friend.
I appreciate it very much!
Gaz
Thank you! Your pointer to Dr. Park brought me some very much needed information.
You see, yesterday I almost had the shape I wanted when a crack developed in the bombardier's nose glazing area. This wasn't even in the area I was hammering, but it immediately turned that piece of aluminum into garbage. My suspect for the problem is improper annealing.
Some metals turn cherry red signifying that they are annealed properly. However, before turning red, aluminum will melt. I've melted a few pieces already. This was a missing piece of the puzzle for me. Most metal working sites work with materials much thicker than mine, because most metal smiths on line are making practical or automotive stuff. However, Dr. Park is using the same roof flashing as me!
Fortunately, Dr. Park has written a practical method on how to ensure your aluminum is properly annealed by the simple expedient of burning or heating away marks made with a red Sharpie.
I will definitely invest more time on learning from Dr. Park.
So, once again, you've improved my modelling knowledge, my friend.
I appreciate it very much!
Gaz
Posted: Friday, August 26, 2016 - 02:56 PM UTC
Hi everyone!
Wow, it's been a while since my last update. And I haven't really accomplished much that is measurable in quality model viewing. So, consider this less and update than a small educational journey I've been taking.
About twelve days ago, I thought I was almost there...then this happened:
So, I had to find more Youtube videos and more useful information and go back to the beginning.

Even though beating on aluminum with a hammer is much quieter than it is with any harder metal, it was enough to irritate my wife at times.
There are a lot of videos on how to make bowls and car panels, but when it comes to stuff this small, there is a lot less to find...or, I don't know the best words to use to search for it. This photo gives an idea of scale compared to say the fender of a car:

Here's how it sits on the model:

Bear in mind, that there is still a lot to do with the piece. Smoothing and shining it. Getting the spaces for the windows out. Shining it again. Making it fit snugly and looking right from every angle. It's added months to the build, I reckon. I hope it will be worth it.
Best Wishes,
Gaz
Wow, it's been a while since my last update. And I haven't really accomplished much that is measurable in quality model viewing. So, consider this less and update than a small educational journey I've been taking.
About twelve days ago, I thought I was almost there...then this happened:

So, I had to find more Youtube videos and more useful information and go back to the beginning.

Even though beating on aluminum with a hammer is much quieter than it is with any harder metal, it was enough to irritate my wife at times.
There are a lot of videos on how to make bowls and car panels, but when it comes to stuff this small, there is a lot less to find...or, I don't know the best words to use to search for it. This photo gives an idea of scale compared to say the fender of a car:

Here's how it sits on the model:

Bear in mind, that there is still a lot to do with the piece. Smoothing and shining it. Getting the spaces for the windows out. Shining it again. Making it fit snugly and looking right from every angle. It's added months to the build, I reckon. I hope it will be worth it.
Best Wishes,
Gaz
Posted: Friday, August 26, 2016 - 06:31 PM UTC
Whoa!! Can't say more other than this might be a job for a CAD/CAM operation in a full-blown manufacturing setting. But then, who has the $$ resources to sub THAT out?

KelticKnot

Joined: May 11, 2015
KitMaker: 768 posts
AeroScale: 656 posts
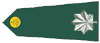
Posted: Friday, August 26, 2016 - 07:09 PM UTC
It looking pretty great so far Gaz.
Have you given thought to how you're going to pierce the window frames without squashing the shape? Or is it quite sturdy once annealed?
Have you given thought to how you're going to pierce the window frames without squashing the shape? Or is it quite sturdy once annealed?

Joel_W


Joined: December 04, 2010
KitMaker: 11,666 posts
AeroScale: 7,410 posts
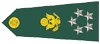
Posted: Friday, August 26, 2016 - 08:30 PM UTC
Gary,
I've been wondering the same as Paul about how you're going to go about cutting out all those panels without damaging the shape of the frame. My other concern as it stands now, the framing is larger in overall dia. then the glass greenhouse. Have you've given this any thought on how you're going to correct it?
Joel
I've been wondering the same as Paul about how you're going to go about cutting out all those panels without damaging the shape of the frame. My other concern as it stands now, the framing is larger in overall dia. then the glass greenhouse. Have you've given this any thought on how you're going to correct it?
Joel
Posted: Saturday, August 27, 2016 - 02:06 AM UTC
Hi guys,
Thank you for your responses.
Brian, I wish I had the money to pay for an expert to do it. On the other hand, it will always be something I've done so if I can get it to a satisfying condition I'll be very pleased with myself. Conversely, if I ruin it, I won't have to cry over lost money.
Paul and Joel, all of those concerns weigh in every time I consider upcoming steps. The piece is nowhere near finished. And can be ruined at any time. Annealing softens the metal making it easier to work. It also makes it easier to accdentally bend. In any case, the part will be not much more resistant to damage than a butterfly's wing. But there is only one way to learn a new skill. Wade-in, do your best, be prepared to start again.
I have some silicon I can pour into the shape once I like where it is. Once it solidifies, it will offer some strength to the shape, while allowing me to pierce the metal if I desire.
Should I run out of patience, there is always paint.
Best wishes,
Gaz
Thank you for your responses.
Brian, I wish I had the money to pay for an expert to do it. On the other hand, it will always be something I've done so if I can get it to a satisfying condition I'll be very pleased with myself. Conversely, if I ruin it, I won't have to cry over lost money.
Paul and Joel, all of those concerns weigh in every time I consider upcoming steps. The piece is nowhere near finished. And can be ruined at any time. Annealing softens the metal making it easier to work. It also makes it easier to accdentally bend. In any case, the part will be not much more resistant to damage than a butterfly's wing. But there is only one way to learn a new skill. Wade-in, do your best, be prepared to start again.
I have some silicon I can pour into the shape once I like where it is. Once it solidifies, it will offer some strength to the shape, while allowing me to pierce the metal if I desire.
Should I run out of patience, there is always paint.
Best wishes,
Gaz
![]() |