World War II
Discuss WWII and the era directly before and after the war from 1935-1949.
Discuss WWII and the era directly before and after the war from 1935-1949.
Hosted by Rowan Baylis
B-29 Superfortress Jumbo King of the Show
Posted: Tuesday, August 30, 2016 - 12:54 PM UTC
Impressive work, Gary. This is really a state of the art all in build.
Posted: Tuesday, August 30, 2016 - 01:42 PM UTC
Jesper,
Thank you! You are really too kind. I'm just trying to learn new techniques to get a desired look.
Gaz
Thank you! You are really too kind. I'm just trying to learn new techniques to get a desired look.
Gaz

KelticKnot

Joined: May 11, 2015
KitMaker: 768 posts
AeroScale: 656 posts
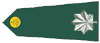
Posted: Tuesday, August 30, 2016 - 04:28 PM UTC
Quoted Text
I have some silicon I can pour into the shape once I like where it is. Once it solidifies, it will offer some strength to the shape, while allowing me to pierce the metal if I desire.
That's what I was starting to think about - whether you could pour something inside to stop the cone collapsing.
I was going to suggest lining the inside with cling film and pouring plaster to give solid support.
Posted: Friday, September 23, 2016 - 04:08 AM UTC
Hi Everyone,
Recently it was put to me: How are you gonna make all of those windows. Until this morning, I considered mechanical means. Drills, knives, scissors, files, and sandpaper.
Then it hit me...how about etching!
I don't have a photo-etch kit. I don't plan on buying one. My first consideration for a caustic substance was bleach. It will eat through aluminum foil in four minutes. In eight minutes you have odd shaped bits of gray floating around in the bleach.
So, I cut a circle of aluminum flashing and dropped it into the bleach then sat down to breakfast. An hour later, the aluminum piece hadn't been eaten through. Obviously I needed something stronger. The only other caustic I have is hydrochloric acid. So, went to Youtube to watch somebody's 3-minute video showing a ball of aluminum foil dissolving into a hot, gray, smoking nothing. Obviously that was too fast for aluminum foil. But this ain't foil, so we'll see what happens to .3mm thick aluminum flashing in the HCL.
By the way... I have hydrochloric acid because I have a saltwater pool. The acid is used to clean mineral deposits from the salt-to-chlorine converter. It's also used to change the pH of the pool water.
Dropping my piece of flashing into the straight HCL, produced a fizzing effect from the aluminum flashing sort of that you might get with a glass of 7-up with an ice cube. That reaction was to grow into a full-blown alka-seltzer type fizzing as lots of hydrogen gas was being created. after five-minutes, the liquid began to turn gray as the aluminum was completely destroyed.
My next test was done with 50-50 HCL-water. The reaction was much slower, and much more controllable. I was able to fish out my test piece of aluminum flashing before it had been destroyed.
So, taking a blowtorch to an old candle I was able to coat a piece of aluminum semi-uniformly with wax. Then I marked a cross-hatch pattern atop the wax with a Sharpie. Each square was roughly 6mmX6mm. Then I cut some of the wax away. I didn't want to get too close to the black lines with my scraper, though in one spot I went way too far.
As the waxed piece of aluminum sat in the mixture of HCL-water, bubbles began to rise from those areas not covered by wax. Eventually, the piece began to roll over and finally dance about in the bubbles as the acid ate through the aluminum in the desired areas. Once the 'dancing' stopped, I lifted the aluminum from the corrosive mixture and dipped it into a bucket of water.

You can see that the right edge of the piece didn't have wax on it, so it was eaten away in that irregular pattern.
Hurriedly, I carved and filed away excess aluminum to completely open two of the 'windows'

So, even though I haven't got the shapes perfect yet, I've got another piece of the puzzle sorted. I'm also happy to have learned that another potentially costly technique can also be done with stuff found at a hardware or pool store for only a few bucks.
Thanks for reading!
Gaz
Recently it was put to me: How are you gonna make all of those windows. Until this morning, I considered mechanical means. Drills, knives, scissors, files, and sandpaper.
Then it hit me...how about etching!
I don't have a photo-etch kit. I don't plan on buying one. My first consideration for a caustic substance was bleach. It will eat through aluminum foil in four minutes. In eight minutes you have odd shaped bits of gray floating around in the bleach.
So, I cut a circle of aluminum flashing and dropped it into the bleach then sat down to breakfast. An hour later, the aluminum piece hadn't been eaten through. Obviously I needed something stronger. The only other caustic I have is hydrochloric acid. So, went to Youtube to watch somebody's 3-minute video showing a ball of aluminum foil dissolving into a hot, gray, smoking nothing. Obviously that was too fast for aluminum foil. But this ain't foil, so we'll see what happens to .3mm thick aluminum flashing in the HCL.
By the way... I have hydrochloric acid because I have a saltwater pool. The acid is used to clean mineral deposits from the salt-to-chlorine converter. It's also used to change the pH of the pool water.
Dropping my piece of flashing into the straight HCL, produced a fizzing effect from the aluminum flashing sort of that you might get with a glass of 7-up with an ice cube. That reaction was to grow into a full-blown alka-seltzer type fizzing as lots of hydrogen gas was being created. after five-minutes, the liquid began to turn gray as the aluminum was completely destroyed.
My next test was done with 50-50 HCL-water. The reaction was much slower, and much more controllable. I was able to fish out my test piece of aluminum flashing before it had been destroyed.
So, taking a blowtorch to an old candle I was able to coat a piece of aluminum semi-uniformly with wax. Then I marked a cross-hatch pattern atop the wax with a Sharpie. Each square was roughly 6mmX6mm. Then I cut some of the wax away. I didn't want to get too close to the black lines with my scraper, though in one spot I went way too far.
As the waxed piece of aluminum sat in the mixture of HCL-water, bubbles began to rise from those areas not covered by wax. Eventually, the piece began to roll over and finally dance about in the bubbles as the acid ate through the aluminum in the desired areas. Once the 'dancing' stopped, I lifted the aluminum from the corrosive mixture and dipped it into a bucket of water.

You can see that the right edge of the piece didn't have wax on it, so it was eaten away in that irregular pattern.
Hurriedly, I carved and filed away excess aluminum to completely open two of the 'windows'

So, even though I haven't got the shapes perfect yet, I've got another piece of the puzzle sorted. I'm also happy to have learned that another potentially costly technique can also be done with stuff found at a hardware or pool store for only a few bucks.
Thanks for reading!
Gaz
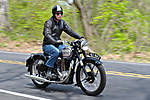
rdt1953

Joined: February 06, 2015
KitMaker: 1,098 posts
AeroScale: 900 posts
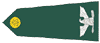
Posted: Friday, September 23, 2016 - 04:45 AM UTC
Gaz -Attaboy ! Think outside the box and push the envelope! Perhaps your resist can be in the form of a mask developed from an expansion - i.e. the representation of a curved surface laid out flat. If you are not familiar with this process there should be something on the internet to guide you . Instruction on drafting and sheet metal development will be most helpful . If I may be of any help let me know- I grew up doing this as my father was a master boat builder and loftsman. You are obviously an extremely capable and industrious guy with a high degree of mechanical aptitude and I admire all you have done - keep at it - you'll get it ! - Richard

Joel_W


Joined: December 04, 2010
KitMaker: 11,666 posts
AeroScale: 7,410 posts
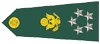
Posted: Friday, September 23, 2016 - 04:49 AM UTC
Gary,
your solution is certainly cutting edge, but seams rather dangerous to me. The end result certainly does produce open panels for what ever means you'll use to make the clear plexi plates.
Have you given it any thought as yet as how to properly size your greenhouse to fit the fuselage as a butt joint, rather then over lapping it?
Joel
your solution is certainly cutting edge, but seams rather dangerous to me. The end result certainly does produce open panels for what ever means you'll use to make the clear plexi plates.
Have you given it any thought as yet as how to properly size your greenhouse to fit the fuselage as a butt joint, rather then over lapping it?
Joel
Posted: Friday, September 23, 2016 - 02:00 PM UTC
Joel,
With eye-protection, good ventilation, and a pool to dive into in case of an acid splash, I've done as much as possible to minimise risk. Yes, I did the entire acid process right beside the pool. I'm not sure what kind of nastiness regular photo etch entails.
Yes, I'm still committed to the overlap strategy. Kind of irrevocably now. And I've learned another metal shaping nuance too: reducing tool marks.
Best wishes,
Gaz
With eye-protection, good ventilation, and a pool to dive into in case of an acid splash, I've done as much as possible to minimise risk. Yes, I did the entire acid process right beside the pool. I'm not sure what kind of nastiness regular photo etch entails.
Yes, I'm still committed to the overlap strategy. Kind of irrevocably now. And I've learned another metal shaping nuance too: reducing tool marks.
Best wishes,
Gaz

Joel_W


Joined: December 04, 2010
KitMaker: 11,666 posts
AeroScale: 7,410 posts
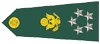
Posted: Friday, September 23, 2016 - 08:52 PM UTC
Gary,
It's the overlapping that concerns me. How do you plan on hiding that overlap where there is none on the real aircraft?
Joel
It's the overlapping that concerns me. How do you plan on hiding that overlap where there is none on the real aircraft?
Joel
Posted: Saturday, September 24, 2016 - 01:00 AM UTC
Hi Gary
When you say you don't want to go down the photo-etching kit route, have you checked out places like Radio Shack? I bought a very cheap set designed for etching circuit boards years ago (OK - I hardly used it after some initial tests (that worked fine) - but that wasn't the set's fault - I just didn't have projects that needed it).
Just to throw another possible solution into the mix... how about carving a pattern for a vacuformed nose, that you could cut sections of foil to fit on?
All the best
Rowan
When you say you don't want to go down the photo-etching kit route, have you checked out places like Radio Shack? I bought a very cheap set designed for etching circuit boards years ago (OK - I hardly used it after some initial tests (that worked fine) - but that wasn't the set's fault - I just didn't have projects that needed it).
Just to throw another possible solution into the mix... how about carving a pattern for a vacuformed nose, that you could cut sections of foil to fit on?
All the best
Rowan

Posted: Saturday, September 24, 2016 - 01:55 AM UTC
Quoted Text
Gary,
It's the overlapping that concerns me. How do you plan on hiding that overlap where there is none on the real aircraft?
Joel
Joel,
To get a smooth surface, I've already removed some of the styrene from the overlapped area. I definitely don't want it to show.
Gaz
Posted: Saturday, September 24, 2016 - 02:27 AM UTC
Quoted Text
Hi Gary
When you say you don't want to go down the photo-etching kit route, have you checked out places like Radio Shack? I bought a very cheap set designed for etching circuit boards years ago (OK - I hardly used it after some initial tests (that worked fine) - but that wasn't the set's fault - I just didn't have projects that needed it).
Just to throw another possible solution into the mix... how about carving a pattern for a vacuformed nose, that you could cut sections of foil to fit on?
All the best
Rowan![]()
Hi Rowan,
Thank you for you suggestions. There are many things I don't know or haven't had the foggiest idea to consider. That being said, everything that is being done now is being done because auminum foil is too fragile to trim in shapes that are acceptable. And I have a reticence to purchasing things I might only use once.
Best wishes,
Gaz
Posted: Saturday, September 24, 2016 - 02:37 AM UTC
Quoted Text
Gaz -Attaboy ! Think outside the box and push the envelope! Perhaps your resist can be in the form of a mask developed from an expansion - i.e. the representation of a curved surface laid out flat. If you are not familiar with this process there should be something on the internet to guide you . Instruction on drafting and sheet metal development will be most helpful . If I may be of any help let me know- I grew up doing this as my father was a master boat builder and loftsman. You are obviously an extremely capable and industrious guy with a high degree of mechanical aptitude and I admire all you have done - keep at it - you'll get it ! - Richard
Richard,
Thank you for your kind words. I know there are a lot of things and methods I don't know. I'd like to know them all, but have only returned to the hobby 2 years ago. Most of what I learn is by trial and error along with info gleaned from the net and other modellers.
Besy wishes,
Gaz
Posted: Saturday, September 24, 2016 - 06:48 PM UTC
Quoted Text
but have only returned to the hobby 2 years ago. Most of what I learn is by trial and error along with info gleaned from the net and other modellers.
Besy wishes,
Gaz
Good heavens! Really? One would never know. How long were you away from the hobby?
The work you are doing on this canopy section is among the most innovative stuff I've ever seen, short of people building entire models from scratch. I have neither the materials talent nor the nerve for such home-made innovation. I admire the fact that you are pursuing this in your own way. Will continue to watch with great interest.

Joel_W


Joined: December 04, 2010
KitMaker: 11,666 posts
AeroScale: 7,410 posts
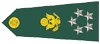
Posted: Sunday, September 25, 2016 - 03:16 AM UTC
Quoted Text
Quoted TextGary,
It's the overlapping that concerns me. How do you plan on hiding that overlap where there is none on the real aircraft?
Joel
Joel,
To get a smooth surface, I've already removed some of the styrene from the overlapped area. I definitely don't want it to show.
Gaz
Gary,
I see. You created a step all the way around, but the way I'm interrupting it, the greenhouse is larger not smaller then the original one.
Joel
Posted: Sunday, September 25, 2016 - 04:00 AM UTC
Quoted Text
Quoted TextHi Gary
When you say you don't want to go down the photo-etching kit route, have you checked out places like Radio Shack? I bought a very cheap set designed for etching circuit boards years ago (OK - I hardly used it after some initial tests (that worked fine) - but that wasn't the set's fault - I just didn't have projects that needed it).
Just to throw another possible solution into the mix... how about carving a pattern for a vacuformed nose, that you could cut sections of foil to fit on?
All the best
Rowan![]()
Hi Rowan,
Thank you for you suggestions. There are many things I don't know or haven't had the foggiest idea to consider. That being said, everything that is being done now is being done because auminum foil is too fragile to trim in shapes that are acceptable. And I have a reticence to purchasing things I might only use once.
Best wishes,
Gaz
Hi Gary
I probably didn't explain what I meant very well - the vacuform could act as a permanent support for the fragile foil, so you could trim it just like you would on a kit's surface.
All the best
Rowan

Posted: Sunday, September 25, 2016 - 02:53 PM UTC
Brian,
As a teen I built a few models between 12 and 14 years old. ...whenever I could scrape up some money. Then I moved to the country and didn't have any money at all until I was 18 and earning a wage. At 20, there were too many other things to do like chasing girls. That was 1985. A couple years ago, i decided to try it again and rediscovered building.
As you know I tend to make things. Without money I was liable to try anything. I once built a glider with toothpicks, looseleaf paper, and wood glue from my granddad's shed. It actually flew after a fashion. Making an aerofoil with toothpicks wasn't easy, or pretty.
Joel,
There was really no other way to go about it that I could be confident about. I hate butt joints.
Rowan,
The whole problem is with hand-steadiness. There's just no way for me to work something so fragile in such an exposed position.
Best wishes,
Gaz
As a teen I built a few models between 12 and 14 years old. ...whenever I could scrape up some money. Then I moved to the country and didn't have any money at all until I was 18 and earning a wage. At 20, there were too many other things to do like chasing girls. That was 1985. A couple years ago, i decided to try it again and rediscovered building.
As you know I tend to make things. Without money I was liable to try anything. I once built a glider with toothpicks, looseleaf paper, and wood glue from my granddad's shed. It actually flew after a fashion. Making an aerofoil with toothpicks wasn't easy, or pretty.
Joel,
There was really no other way to go about it that I could be confident about. I hate butt joints.
Rowan,
The whole problem is with hand-steadiness. There's just no way for me to work something so fragile in such an exposed position.
Best wishes,
Gaz
Posted: Wednesday, October 12, 2016 - 10:14 AM UTC
Hi everyone!
My metal education continues, with some headway made recently. Here's where we are at the moment:

I've wasted a lot of time doing things the wrong way.
Here's another image to give you some scale:

There are still many tasks that can turn this shape into just another piece of scrap. In a place where you can't see is a crater I didn't know about until I polished it for this update.
I'd really like to complete this puppy before next year. But I'm running out of time.
In the "new tool" category I present this bench sander:

My powerful angle grinder and it's many discs have made the bench grinder obsolete. Instead of trimming the edge micrometers at a time with an easy-to-dull blade, I've been able to use this stationary sander to take away small bits of aluminum until I got it to fit. All I needed was to remove the grinding disc, replace it with a 20mm thick piece of pine cut into a 6-inch disc, and a pack of orbital sander discs. A 7-dollar (the cost of the sanding discs) cost instead of buying a tool that would cost well over 100 bucks.
Best Wishes, Everyone!
Gaz
My metal education continues, with some headway made recently. Here's where we are at the moment:

I've wasted a lot of time doing things the wrong way.
Here's another image to give you some scale:

There are still many tasks that can turn this shape into just another piece of scrap. In a place where you can't see is a crater I didn't know about until I polished it for this update.
I'd really like to complete this puppy before next year. But I'm running out of time.
In the "new tool" category I present this bench sander:

My powerful angle grinder and it's many discs have made the bench grinder obsolete. Instead of trimming the edge micrometers at a time with an easy-to-dull blade, I've been able to use this stationary sander to take away small bits of aluminum until I got it to fit. All I needed was to remove the grinding disc, replace it with a 20mm thick piece of pine cut into a 6-inch disc, and a pack of orbital sander discs. A 7-dollar (the cost of the sanding discs) cost instead of buying a tool that would cost well over 100 bucks.
Best Wishes, Everyone!
Gaz

goodn8

Joined: October 12, 2008
KitMaker: 709 posts
AeroScale: 651 posts

Posted: Wednesday, October 12, 2016 - 11:18 AM UTC
Great craftsmanship, Gary!
The nose fits very well, wonder how this will look finally.
Always a pleasure to check your thread an updates. Everytime something new, innovative and improvised. Love that way to use and modify existing things if possible to save money.
Thomas
The nose fits very well, wonder how this will look finally.
Always a pleasure to check your thread an updates. Everytime something new, innovative and improvised. Love that way to use and modify existing things if possible to save money.

Thomas

Posted: Wednesday, October 12, 2016 - 02:04 PM UTC
An extraordinary effort, Gaz! I would say obsessive, but who am I to talk?

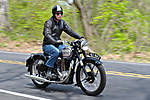
rdt1953

Joined: February 06, 2015
KitMaker: 1,098 posts
AeroScale: 900 posts
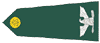
Posted: Wednesday, October 12, 2016 - 04:05 PM UTC
Gary - The greenhouse looks great ! As far as the smoothing goes, perhaps you could make a miniature English Wheel using a C - clamp as the basis for the frame.
A slot in the fixed foot for one wheel and a bracket and wheel on the threaded shaft replacing that foot might do it . Access to a lathe would be helpful for turning wheels to to various diameters and contours. There should be plenty on the Internet about English Wheels and their use .
Watching with great interest- Richard
A slot in the fixed foot for one wheel and a bracket and wheel on the threaded shaft replacing that foot might do it . Access to a lathe would be helpful for turning wheels to to various diameters and contours. There should be plenty on the Internet about English Wheels and their use .
Watching with great interest- Richard

Joel_W


Joined: December 04, 2010
KitMaker: 11,666 posts
AeroScale: 7,410 posts
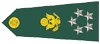
Posted: Wednesday, October 12, 2016 - 09:22 PM UTC
Gary,
Outstanding progress way past the point I'd honestly ever thought you'd get. I'm pretty sure I can see that depression on the far side. The fit looks excellent, and I can see it's now see how the nose clip fits into the step you've made.
If I remember correctly, you're going to smooth it out using a hammer?
Have you figured out how to layout and then cut out all those window frames?
Joel
Outstanding progress way past the point I'd honestly ever thought you'd get. I'm pretty sure I can see that depression on the far side. The fit looks excellent, and I can see it's now see how the nose clip fits into the step you've made.
If I remember correctly, you're going to smooth it out using a hammer?
Have you figured out how to layout and then cut out all those window frames?
Joel
Posted: Wednesday, October 12, 2016 - 11:53 PM UTC
Thomas,
Thank you very much! It's fun just to explore the limits of my abilities. I'm glad you ar enjoying the process.
Brian,
Thank you! Expanding my metal skills is a pursuit that I find interesting as well as hopefully a way to become a metal shaping artist. As far as the bomber goes, I still hope to complete mine before Next Christmas.
Richard,
Thank you. I'll give the miniature English wheel some contemplation. I've read from metal shaping sites that mastering the art with hand tools will better prepare one for using larger and power tools later.
Joel,
Thank you! Working with metal is like walking near a cliff. There is only one mistake between success and abject failure. And I still have many steps to go.
I have the AM windows for the glasshouse that I will use as a template. With the piece dry-fitted, I'll measure and mark and also judge by eye what looks best. ...and hopefully avoid walking over that cliff.
Still, once the planishing is done I will have to adjust the shape of the piece. Because, even the slightest, gentlest tap of the hammer moves metal. I planished for a while last night, and have already noticed small changes.
Best wishes,
Gaz
Thank you very much! It's fun just to explore the limits of my abilities. I'm glad you ar enjoying the process.
Brian,
Thank you! Expanding my metal skills is a pursuit that I find interesting as well as hopefully a way to become a metal shaping artist. As far as the bomber goes, I still hope to complete mine before Next Christmas.
Richard,
Thank you. I'll give the miniature English wheel some contemplation. I've read from metal shaping sites that mastering the art with hand tools will better prepare one for using larger and power tools later.
Joel,
Thank you! Working with metal is like walking near a cliff. There is only one mistake between success and abject failure. And I still have many steps to go.
I have the AM windows for the glasshouse that I will use as a template. With the piece dry-fitted, I'll measure and mark and also judge by eye what looks best. ...and hopefully avoid walking over that cliff.
Still, once the planishing is done I will have to adjust the shape of the piece. Because, even the slightest, gentlest tap of the hammer moves metal. I planished for a while last night, and have already noticed small changes.
Best wishes,
Gaz
Posted: Friday, October 14, 2016 - 07:50 AM UTC
Wow Gary! your persistence with this is absolutely astounding and really paying off!
have you considered using wet/dry sand paper to remove the hammer marks, working from a coarse grade through to finer and finer grades, until you achieve the NMF gloss desired?

have you considered using wet/dry sand paper to remove the hammer marks, working from a coarse grade through to finer and finer grades, until you achieve the NMF gloss desired?

Posted: Friday, October 14, 2016 - 11:11 AM UTC
HI Russell,
Thank you very much! I'm glad that you like it so far.
I have considered abrasives, but that path is fraught with more chances for ruining it than making it come out as desired.
Remember, it is only .3mil thick. And in some places may be thinner. If I were to cut it in half, it would look like a cross section of the of the surface of the ocean. Imagine trying to sand a surface like that down without going through.
And in truth, working metal is something I would like to do. I have always had a thing for scratch building stuff. Being able to turn metal into self-supporting 3d structures is something I feel I need to know. So this single piece on this model is like the first step into the future.
Anyway, here are some pictures.
I've probably spent about 12 hours working on this piece since the previous update. It is much smoother now that it was then.

Aluminum polish allows me to highlight the areas that need work. Every low spot shows up as dark gray against the pure shine of the Alu. The polish not only smooths roughness on the surface, it also removes oxidation. All of those gray-black areas are oxidized metal.
You've seen King Tut's Gold mask from the sarcophagus? That was all done with a hammer. So, I need to attain that perfect smoothness with a hammer as well. hopefully, a couple thousand years removed, my tools are better than theirs.
Best Wishes,
Gaz
Thank you very much! I'm glad that you like it so far.
I have considered abrasives, but that path is fraught with more chances for ruining it than making it come out as desired.
Remember, it is only .3mil thick. And in some places may be thinner. If I were to cut it in half, it would look like a cross section of the of the surface of the ocean. Imagine trying to sand a surface like that down without going through.
And in truth, working metal is something I would like to do. I have always had a thing for scratch building stuff. Being able to turn metal into self-supporting 3d structures is something I feel I need to know. So this single piece on this model is like the first step into the future.
Anyway, here are some pictures.

I've probably spent about 12 hours working on this piece since the previous update. It is much smoother now that it was then.

Aluminum polish allows me to highlight the areas that need work. Every low spot shows up as dark gray against the pure shine of the Alu. The polish not only smooths roughness on the surface, it also removes oxidation. All of those gray-black areas are oxidized metal.

You've seen King Tut's Gold mask from the sarcophagus? That was all done with a hammer. So, I need to attain that perfect smoothness with a hammer as well. hopefully, a couple thousand years removed, my tools are better than theirs.
Best Wishes,
Gaz

KelticKnot

Joined: May 11, 2015
KitMaker: 768 posts
AeroScale: 656 posts
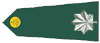
Posted: Friday, October 14, 2016 - 01:19 PM UTC
Its looking great Gaz, you're certainly moving in the right direction. I think you've got the technique down so its just a matter of repeating till you're happy with the result.
![]() |